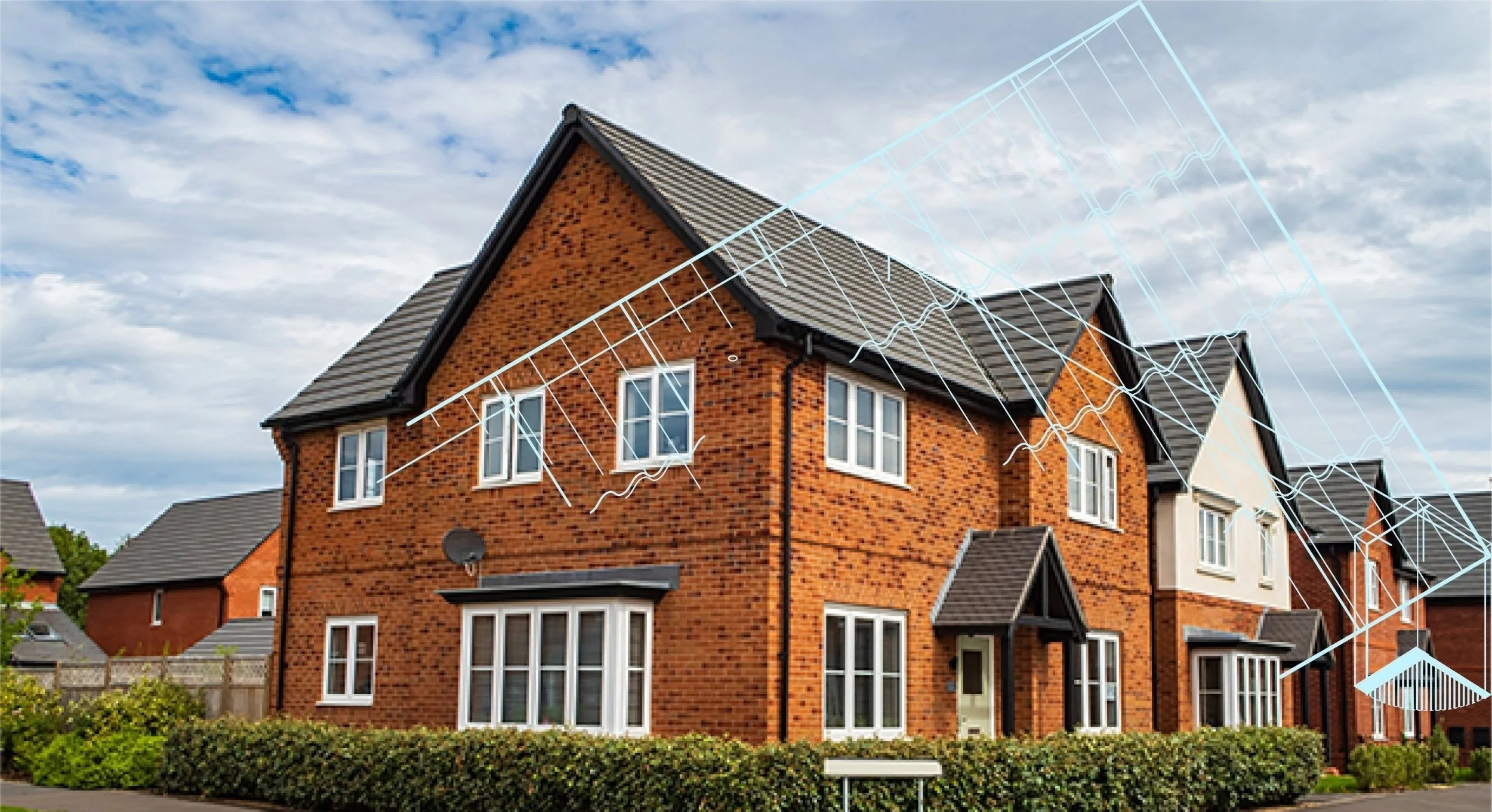
The Complete Door Canopy Guide
A comprehensive guide to choosing, installing, and maintaining door canopies for UK homes
Table of Contents
1. What is a Door Canopy?
Door canopies represent one of the most practical and cost-effective exterior home improvements available to UK homeowners. At its core, a door canopy is a protective roof structure installed above exterior doors, designed to shield against Britain's unpredictable weather whilst simultaneously enhancing your property's kerb appeal. Unlike major renovations that require weeks of disruption and substantial investment, a quality door canopy transforms your entrance in hours, providing immediate weather protection and visual impact. As manufacturers who've been crafting canopies for UK homes for years, we've witnessed countless transformations where a simple canopy installation has elevated ordinary entrances into welcoming focal points. The beauty lies in their versatility - whether you're protecting a cottage door from driving rain or adding architectural interest to a modern build, the right canopy serves both form and function brilliantly.
Understanding the Terminology
Door canopies go by several names, often causing confusion for homeowners researching options. The most common terms you'll encounter include front door canopy and over door canopy, which describe the basic function of providing overhead protection. Porch canopy typically refers to more substantial structures that might incorporate side elements or extended coverage, whilst door awning usually describes lighter, sometimes retractable designs more commonly found on commercial properties. The term portico traditionally describes grand, columned entrances often found on Georgian or Victorian properties, though modern interpretations use lightweight materials to achieve similar visual impact without structural complexity. Understanding these distinctions helps when discussing requirements with suppliers and ensures you're comparing like-for-like products.
Why Install a Door Canopy?
Immediate Weather Protection Britain's maritime climate delivers rain on approximately 150 days annually, with sudden downpours capable of soaking anyone caught at their front door. A properly designed canopy provides essential shelter whilst you fumble for keys, unload shopping, or welcome guests. For families with young children or elderly relatives, this protection proves invaluable during winter months when wet steps become treacherous. The peace of mind that comes with knowing your entrance remains accessible regardless of weather conditions represents significant practical value that most homeowners appreciate immediately after installation.
Enhanced Kerb Appeal and Property Value Estate agents consistently emphasise kerb appeal's importance in property valuations, with first impressions significantly influencing buyer interest. A thoughtfully chosen canopy transforms plain entrances into attractive focal points that suggest care and attention to detail throughout the property. Our experience shows that homes with quality canopies often receive more viewing requests and achieve faster sales. The investment typically pays for itself through increased property value, making this improvement both practically and financially sensible.
Door and Frame Protection Your front door endures constant exposure to UV radiation, driving rain, and temperature fluctuations that gradually degrade even high-quality materials. Wooden doors suffer particularly, with unprotected timber prone to warping, splitting, and paint failure. Even modern composite and uPVC doors benefit from overhead protection that reduces thermal cycling and prevents weather-related deterioration. A canopy acts as the first line of defence, potentially extending your door's lifespan by years whilst maintaining its appearance.
Cost-Effective Home Improvement Unlike extensions, conversions, or major renovations, canopy installation represents exceptional value for money. Most installations complete within half a day, providing immediate transformation without the disruption, planning complications, or substantial costs associated with larger projects. The relatively modest investment delivers disproportionate visual impact, making canopies popular with homeowners seeking maximum improvement for minimal outlay.
Which Properties Benefit Most?
New Builds and Modern Homes Contemporary properties often feature clean lines and minimal architectural detail that, whilst appealing, can appear stark or unwelcoming. A carefully selected canopy adds definition and character without overwhelming the design aesthetic. Modern flat canopies or minimalist apex designs complement geometric facades perfectly, providing weather protection whilst maintaining architectural integrity. The addition helps new builds feel more established and welcoming.
Period Properties Victorian, Edwardian, and Georgian homes possess inherent character that appropriate canopies can enhance beautifully. Traditional timber canopies or high-quality composite alternatives that mimic period detailing complement existing architectural features whilst providing modern weather protection standards. The key lies in selecting designs that respect historical proportions and materials whilst delivering contemporary performance.
Exposed Locations Properties facing prevailing winds, situated on hills, or lacking natural shelter from trees or neighbouring buildings gain enormous practical benefit from canopy installation. In these locations, the weather protection aspect often outweighs aesthetic considerations, though modern designs successfully combine both attributes. Coastal properties particularly benefit from the additional protection against salt-laden winds that can accelerate deterioration of doors and frames.
Protection from UK Weather Conditions
The UK's maritime climate presents unique challenges that quality canopies must address effectively. With regional variations from the wet Scottish Highlands to the milder Southwest, canopies need robust construction and weather-resistant materials to perform reliably across diverse conditions.
Rain and Wind Resistance British weather patterns frequently combine driving rain with gusting winds, creating challenging conditions that inferior canopies struggle to handle. Our manufacturing process specifically addresses these requirements through rigorous testing and quality control measures. We subject our designs to simulated wind loads exceeding typical storm conditions, ensuring brackets remain secure and structures maintain integrity even in severe weather. Proper installation into suitable wall substrates proves equally critical, which is why we provide detailed guidance for different wall types commonly found in UK construction.
Cold Weather Performance Winter conditions test canopy materials through freeze-thaw cycles that can crack inferior products or loosen inadequately secured fixings. Quality materials like our composite formulations maintain flexibility and strength throughout temperature variations, whilst galvanised steel brackets resist corrosion even when exposed to road salt and harsh winter conditions. Snow loading, whilst rarely extreme in most UK regions, still requires consideration in canopy design, particularly for larger structures.
UV Protection Capabilities Even British sunshine gradually degrades unprotected materials, causing fading, chalking, and eventual structural deterioration. Our manufacturing incorporates UV-stabilised pigments throughout the material thickness, ensuring colour consistency for decades rather than surface treatments that wear away over time. This attention to detail explains why our canopies maintain their appearance long after cheaper alternatives have faded or discoloured.
Table of Contents
2. Types of Door Canopies
The door canopy market offers numerous styles, each designed to serve specific architectural contexts and practical requirements. Understanding these variations helps homeowners select designs that complement their property's character whilst providing optimal weather protection. Over our years of manufacturing, we've refined classic designs and developed contemporary alternatives that meet modern performance standards without compromising aesthetic appeal. The key to successful canopy selection lies in matching the design's visual weight and style to your property's architecture whilst ensuring the structure provides adequate coverage for your specific entrance configuration. Whether you're drawn to traditional pitched roofs that echo classic British architecture or prefer contemporary flat designs that complement modern builds, the right choice enhances both your home's appearance and your daily comfort. Each style offers distinct advantages in terms of weather protection, visual impact, and installation requirements that we'll explore in detail.
Contemporary Flat Door Canopy
Contemporary flat canopies embody modern architectural principles of clean lines, minimal ornamentation, and functional beauty. These designs suit properties where traditional pitched roofs might appear incongruous or overwhelming, particularly modern builds with geometric facades and large glazed areas. The flat profile offers practical advantages including reduced visual bulk and easier integration with existing building features like lighting or security systems.
Despite their simple appearance, quality flat canopies require sophisticated engineering to ensure effective water drainage and structural integrity. Our designs incorporate subtle slopes invisible to the casual observer but essential for preventing water accumulation and ensuring longevity. The minimal aesthetic relies on precise manufacturing and quality materials to achieve the refined appearance that characterises successful contemporary design.
Construction and Materials: Modern flat canopies utilise advanced materials like powder-coated aluminium, architectural-grade GRP, or our proprietary composite formulations. These materials offer superior weather resistance compared to traditional options whilst enabling the clean finishes essential to contemporary design. Hidden fixings maintain the minimalist aesthetic whilst ensuring structural security.
Best Applications:
New builds and architect-designed homes
Properties with strong horizontal emphasis
Minimalist or Scandinavian-influenced designs
Situations where traditional canopies might appear incongruous
Homeowners prioritising low-maintenance solutions
Shop Contemporary Flat Door canopies
Decorative Flat Canopy
Decorative flat canopies bridge traditional and contemporary design approaches by combining flat roof practicality with ornamental elements. These versatile designs suit properties where pure minimalism might appear too stark whilst avoiding the visual weight of fully pitched designs. Decorative elements might include carved brackets, moulded edge details, or subtle texture that adds visual interest without overwhelming the entrance.
The success of decorative flat canopies depends on restraint and proportion. Over-elaborate details can appear fussy, whilst insufficient decoration fails to justify the departure from pure contemporary styling. Our designs achieve balance through carefully scaled elements that enhance rather than dominate the overall composition.
Design Elements: Common decorative features include scrolled brackets reminiscent of traditional ironwork, dentil moulding along the canopy edge, or subtle surface texturing that creates shadow lines. These elements can be integral to GRP or composite construction or added as separate components for timber canopies.
Suitable Properties:
Traditional properties requiring weather protection without full period styling
Modern homes needing softened architectural lines
Transitional architectural styles
Properties where neighbours have varied canopy styles
Pitched Door Canopy (Mono-Pitch)
The mono-pitch or lean-to canopy offers excellent weather protection through its single-slope design whilst maintaining relatively modest visual impact. Water drainage proves superior to flat designs, whilst the angled profile creates attractive shadow lines that add depth to entrance areas. This style suits a broad range of property types and represents an excellent compromise between traditional and contemporary approaches.
Mono-pitch canopies work particularly well on properties with strong directional emphasis or where full apex designs might appear disproportionate. The single slope can echo roof lines elsewhere on the building, creating pleasing visual relationships that integrate the canopy naturally with existing architecture.
Technical Advantages: The sloped design ensures positive water drainage without requiring complex gutter systems. Snow shedding proves efficient, reducing loading concerns in areas prone to accumulation. The asymmetrical profile offers design flexibility whilst maintaining structural simplicity.
Construction Variations: Mono-pitch canopies can feature exposed or concealed brackets depending on the desired aesthetic. Projection depths vary considerably, allowing customisation for specific protection requirements. Materials range from traditional timber to modern composites, each offering distinct appearance and maintenance characteristics.
Apex Door Canopy
Apex canopies represent the quintessential British door canopy style, featuring the classic triangular profile that echoes traditional roof construction. This design offers maximum weather protection through generous coverage and efficient water management whilst creating strong architectural presence that enhances property character. The twin-slope configuration provides excellent structural stability and distributes loads effectively across supporting brackets.
Our apex canopies reflect years of design refinement, with proportions derived from classical architecture and adapted for modern manufacturing techniques. The result combines authentic appearance with contemporary performance standards and installation convenience.
Design Heritage: The apex form derives from fundamental principles of British architecture, where pitched roofs have provided reliable weather protection for centuries. Modern interpretations maintain these proportional relationships whilst incorporating advanced materials and manufacturing techniques that ensure longevity and reduce maintenance requirements.
Construction Details: Quality apex canopies feature properly proportioned ridge lines, appropriate eave details, and robust bracket systems capable of supporting the structure's weight plus anticipated weather loads. Our designs incorporate traditional elements like finials and bargeboards where appropriate whilst ensuring compatibility with modern installation techniques.
Suitability: Apex canopies suit virtually all property types but prove particularly effective on traditional British housing styles including Victorian terraces, Edwardian semis, and cottage-style properties. The substantial coverage makes them ideal for exposed locations or where maximum weather protection is prioritised.
Bell Curve Door Canopy
The bell curve or bell cast canopy features distinctive flared profiles that sweep outward near the base, creating elegant curves whilst directing water away from entrance areas. This sophisticated design suits heritage properties and adds architectural interest without the visual weight of fully pitched alternatives. The curved profile requires skilled manufacturing to achieve smooth, consistent lines that maintain their appearance over time.
Bell curve canopies work particularly well on Victorian and Edwardian properties where the flowing lines complement period architectural details. The distinctive profile creates attractive shadow patterns that enhance entrance areas throughout the day.
Manufacturing Challenges: Creating smooth, consistent curves requires precision moulding techniques and quality materials capable of holding complex shapes without distortion. Our GRP and composite manufacturing processes excel in producing these demanding profiles whilst ensuring long-term dimensional stability.
Period Authenticity: Historical bell cast canopies were typically constructed from lead or copper, materials that developed attractive patinas but required extensive maintenance. Modern alternatives achieve similar visual effects whilst providing superior weather resistance and reduced maintenance requirements.
Enquire about Bell Curve Door Canopies
Georgian and Edwardian Canopies
Period-inspired canopies reflect the architectural principles and proportional systems of their respective eras whilst incorporating modern materials and manufacturing techniques. Georgian designs emphasise symmetry, classical proportions, and refined detailing derived from ancient architectural orders. Edwardian styles build upon Georgian foundations whilst incorporating slightly simplified details and acknowledging emerging modern influences.
Successful period canopies require careful attention to historical precedent combined with practical considerations of modern installation and maintenance. The challenge lies in achieving authentic appearance whilst meeting contemporary performance expectations and building standards.
Georgian Characteristics: Georgian canopies typically feature mathematical proportions, refined moulding profiles, and details that reference classical architecture. Bracket designs might incorporate elements reminiscent of stone corbels or timber brackets found on period buildings. Colour schemes favour traditional whites, creams, or heritage colours appropriate to the period.
Edwardian Evolution: Edwardian designs maintain period character whilst showing greater simplicity and acknowledgment of changing tastes. Details become less elaborate whilst retaining essential proportional relationships. This style often suits homeowners seeking period character without full Georgian formality.
Arched Canopy
Arched canopies feature gentle curves that create soft, flowing profiles suitable for both traditional and contemporary applications. The curved form offers practical advantages including excellent water management and reduced wind resistance whilst providing visually appealing alternatives to angular designs. Manufacturing quality proves critical in achieving smooth, consistent curves that maintain their appearance over extended periods.
The versatility of arched designs allows interpretation in various materials and detail levels. Simple curves suit modern applications whilst more elaborate profiles complement traditional architecture. The key lies in selecting appropriate radius and detail levels for specific applications.
Structural Considerations: Curved profiles require careful engineering to ensure adequate strength whilst maintaining the flowing lines essential to the design's success. Our manufacturing techniques ensure consistent wall thickness and appropriate reinforcement without compromising the aesthetic quality.
Design Flexibility: Arched canopies can be subtle or dramatic depending on the curve radius and overall proportions. Gentle curves create sophisticated understatement whilst more pronounced profiles make bold architectural statements.
Portico
Porticos represent the grandest canopy option, featuring substantial roof coverage supported by columns or substantial brackets. Traditional porticos were significant architectural features that announced important entrances whilst providing extensive weather protection. Modern interpretations achieve similar visual impact through lightweight materials and simplified construction techniques.
Contemporary porticos suit larger properties where substantial entrance features appear proportionate. They work particularly well on detached houses with generous frontages or properties requiring maximum weather protection for practical or aesthetic reasons.
Modern Adaptations: Traditional stone or timber porticos required substantial structural support and represented major construction projects. Modern alternatives use lightweight materials and simplified support systems whilst maintaining the visual impact that makes porticos so appealing.
Suitability Considerations: Porticos require careful scale consideration to avoid overwhelming smaller properties. They work best where substantial entrance features appear natural and proportionate. Planning permission may be required for larger structures, particularly in conservation areas or on listed buildings.
Table of Contents
3. Choosing the Right Material
Material selection fundamentally determines your canopy's appearance, longevity, maintenance requirements, and overall value. Having manufactured thousands of canopies using various materials, we've gained deep insight into how different options perform across the diverse conditions encountered in UK climates. The choice extends beyond simple aesthetic preferences to encompass practical considerations including maintenance commitment, local weather exposure, and long-term cost implications. Modern manufacturing techniques have transformed traditional materials whilst introducing entirely new options that combine the best characteristics of multiple approaches. Our experience demonstrates that informed material selection, based on realistic assessment of your priorities and circumstances, leads to greater satisfaction than decisions based solely on initial cost or appearance. Quality materials justify their premium through superior performance, reduced maintenance, and enhanced durability that provides genuine long-term value.
Composite Polymer - Our Speciality
Composite polymer represents the culmination of advanced materials science applied to door canopy manufacturing. Our proprietary composite formulations combine multiple materials to achieve performance characteristics impossible with single-material approaches. Unlike simple plastic products, our composites incorporate carefully selected reinforcement fibres, UV stabilisers, and impact modifiers that ensure decades of reliable performance across all UK weather conditions.
Advanced Manufacturing Process: Our composite canopies are created through precision injection moulding that ensures consistent material distribution and eliminates the weak points common in hand-laid alternatives. The process allows complex geometries with integral fixing points, drainage channels, and decorative details that would be expensive or impossible to achieve through traditional construction methods. Quality control at every stage ensures each canopy meets our exacting standards before leaving the factory.
Performance Characteristics:
Exceptional Durability: 25-30 year lifespan with minimal maintenance
Colour Stability: Integral pigmentation prevents fading and maintains appearance
Impact Resistance: Withstands accidental damage that might crack or dent alternatives
Thermal Stability: Maintains properties across extreme temperature ranges
Weather Resistance: Unaffected by UV, rain, frost, or atmospheric pollution
Maintenance Advantages: Composite canopies require only occasional cleaning with mild detergent and water. The material won't rot, rust, or degrade, eliminating the ongoing treatment costs associated with timber alternatives. Scratches don't expose different coloured substrates since pigmentation extends throughout the material thickness.
Design Flexibility: Our manufacturing process enables complex profiles, integral decorative details, and precise colour matching impossible with traditional materials. Custom colours, textures, and finishes allow exact coordination with existing building elements whilst maintaining all performance advantages.
Shop Composite Polymer Door Canopies
GRP (Glass Reinforced Plastic)
GRP combines exceptional strength with design versatility, allowing complex shapes and detailed mouldings that enhance both appearance and functionality. Our GRP manufacturing utilises hand-laid techniques that optimise fibre orientation for maximum strength whilst achieving superior surface finishes through automotive-grade gel coats.
Technical Advantages: GRP's reinforcement fibres provide excellent impact resistance and structural integrity that won't deteriorate over time. The material remains unaffected by moisture, insects, or atmospheric pollution that degrades natural alternatives. Thermal expansion coefficients remain low, reducing stress on fixings and maintaining dimensional stability.
Manufacturing Excellence: Our GRP process begins with precision moulds that ensure consistent quality and detailed reproduction of design elements. Hand-laid construction allows optimal fibre placement for maximum strength whilst maintaining smooth, professional finishes. Multiple gel coat applications provide depth and durability impossible with painted surfaces.
Applications: GRP excels in applications requiring complex curves, detailed mouldings, or maximum weather resistance. The material's strength-to-weight ratio makes it ideal for larger canopies whilst detailed moulding capabilities suit traditional designs requiring authentic period character.
Timber - Traditional Excellence
Properly specified and maintained timber canopies offer unmatched natural beauty and authentic character that many homeowners find irreplaceable. Our timber canopies utilise sustainably sourced hardwoods and premium softwoods treated to resist moisture, insects, and decay whilst maintaining the working characteristics that make timber so appealing.
Species Selection: Different timber species offer varying characteristics that suit specific applications. Oak provides exceptional durability and attractive grain patterns but commands premium prices. Treated pine offers cost-effective solutions when properly maintained, whilst exotic hardwoods provide unique colours and grain patterns for special applications.
Treatment and Protection: Modern timber treatments significantly enhance performance whilst maintaining natural appearance. Pressure-treated options resist moisture and insect attack, whilst transparent stains allow natural grain patterns to show through protective barriers. Regular maintenance remains essential but modern products reduce frequency and simplify application.
Maintenance Requirements: Timber canopies require annual inspection and treatment every 12-18 months depending on exposure levels. Quality exterior wood preservatives penetrate deeply to provide lasting protection, whilst regular cleaning prevents moisture accumulation that encourages decay. The maintenance commitment suits homeowners who appreciate natural materials and take satisfaction from caring for their property.
Character Development: Properly maintained timber develops attractive weathered patinas that enhance rather than detract from appearance. The natural aging process creates unique character impossible to replicate artificially, making each canopy distinctive whilst maintaining structural integrity.
Aluminium - Modern Performance
Powder-coated aluminium offers exceptional strength-to-weight ratios and corrosion resistance that suit modern architectural applications. The material's versatility allows both simple geometric designs and complex fabricated structures whilst maintaining consistent performance across all UK climate zones.
Corrosion Resistance: Aluminium naturally forms protective oxide layers that prevent corrosion even in coastal environments. Powder coating provides additional protection whilst enabling extensive colour options that maintain consistency for decades. The combination ensures maintenance-free performance in applications where steel might require ongoing attention.
Design Capabilities: Modern aluminium fabrication techniques enable complex geometries, integrated drainage systems, and precise dimensional control impossible with cast or moulded alternatives. Welded construction provides seamless joints whilst maintaining structural integrity under all loading conditions.
Sustainability: Aluminium's recyclability and energy-efficient production methods appeal to environmentally conscious homeowners. The material's longevity and maintenance-free performance contribute to reduced lifetime environmental impact compared to alternatives requiring ongoing treatment or replacement.
Polycarbonate - Cost-Effective Solutions
Polycarbonate sheet materials provide transparent or translucent coverage that allows natural light whilst maintaining weather protection. The material's impact resistance and light weight make it suitable for DIY installation whilst costs remain modest compared to premium alternatives.
Transparency Options: Clear polycarbonate maximises light transmission whilst maintaining weather protection. Tinted options reduce solar heat gain whilst maintaining visibility. Opaque versions provide privacy whilst allowing diffused light to illuminate entrance areas.
Installation Advantages: Polycarbonate's light weight simplifies installation and reduces structural requirements. Standard sheet sizes suit common canopy dimensions whilst cutting and drilling require only basic tools. The material's flexibility accommodates minor dimensional variations without stress concentration.
Performance Limitations: UV exposure gradually reduces clarity and can cause yellowing in lower-quality grades. Impact resistance, whilst good, doesn't match solid alternatives. Thermal expansion requires careful detailing to prevent stress concentration at fixing points.
Steel - Industrial Strength
Powder-coated steel provides maximum strength for applications requiring substantial load-bearing capacity or resistance to vandalism. The material suits commercial applications or residential installations where security and durability outweigh weight considerations.
Coating Technology: Modern powder coating systems provide superior protection compared to traditional paint finishes. The electrostatically applied coating forms strong chemical bonds with the steel substrate whilst providing consistent thickness and appearance. Quality systems resist impact, UV exposure, and atmospheric pollution.
Fabrication Capabilities: Steel's strength enables complex fabricated structures with minimal material thickness. Welded construction provides permanent joints whilst maintaining access for coating application. Precision fabrication ensures proper fit and professional appearance.
Maintenance Considerations: Quality powder coating maintains appearance for decades with minimal care. However, damage to the coating system requires prompt attention to prevent corrosion spread. Regular inspection and touch-up of minor damage ensures long-term performance.
Material | Lifespan | Maintenance | Cost Range | Best Applications |
---|---|---|---|---|
Composite | 25-30 years | Minimal | ££ | All property types |
GRP | 30+ years | Minimal | ££ | Complex shapes, detail |
Timber | 15-25 years | Regular | £££ | Period properties |
Aluminium | 25-40 years | Minimal | ££ | Modern designs |
Polycarbonate | 10-20 years | Basic | £ | Budget applications |
Steel | 20-30 years | Moderate | £££ | High-strength needs |
Table of Contents
4. Standard Door Canopy Sizes
Selecting appropriate canopy dimensions requires careful consideration of door proportions, available wall space, and desired coverage levels. Standard UK front doors typically measure 762mm wide by 1981mm high (2'6" x 6'6"), though modern properties increasingly feature wider doors up to 838mm or even 1000mm for enhanced accessibility. Understanding these baseline dimensions helps inform canopy sizing decisions, but simply matching door width rarely provides optimal results. you can get a quick-summary on how to choose the best door canopy size guide.
Effective canopy design extends beyond the door opening to protect surrounding areas, accommodate visitors, and create pleasing visual proportions that enhance rather than overwhelm your entrance. Our manufacturing experience demonstrates that slightly oversized canopies generally prove more satisfactory than minimal coverage, providing better weather protection whilst creating more substantial architectural presence. However, exceeding available wall space or ignoring planning restrictions can create problems that careful measurement and planning easily avoid.
Understanding Door and Wall Measurements
Accurate measurement forms the foundation of successful canopy selection. Begin by measuring your door opening including the frame, noting any protruding elements like letter boxes or decorative mouldings that might affect canopy clearance. Measure available wall space on either side of the door, identifying nearby features like windows, downpipes, or lighting that could influence canopy positioning.
Critical Measurements:
Door width including frame
Available wall width for bracket positioning
Height from door head to any overhead obstructions
Wall projection space without encroaching on boundaries
Distance to neighbouring features requiring clearance
Common Measurement Errors: Many homeowners measure only the door leaf width, ignoring frame dimensions that can add 100mm or more to the opening. Others overlook protruding door furniture or decorative elements that require additional clearance. Always measure the complete opening width plus desired overhang on each side.
Standard Canopy Widths and Projections
Our standard canopy widths progress in logical increments that suit common UK door configurations whilst accommodating various coverage preferences. Smaller canopies suit budget-conscious homeowners or properties with space constraints, whilst larger options provide generous coverage for exposed locations or grander architectural effects.
Standard Width Options:
1000mm: Suitable for narrow doors or space-constrained installations
1200mm: Popular choice for standard doors with modest overhang
1400mm: Generous coverage for standard doors or narrow double doors
1600mm: Wide single doors or narrow double door applications
1800mm: Double doors or substantial single door coverage
2000mm+: Grand entrances or maximum coverage requirements
Projection Considerations: Standard projections range from 450mm for minimal coverage to 1000mm for maximum protection. Deeper projections provide better weather protection but require stronger bracket systems and may trigger planning considerations if exceeding 1000mm from the wall face.
Specific Product Dimensions
Our Apex Door Canopies represent our most popular range, offering traditional styling with modern performance. Available in five standard widths, each provides specific coverage characteristics suited to different applications.
Specific Product Dimensions
Our Apex Door Canopies represent our most popular range, offering traditional styling with modern performance. Available in five standard widths, each provides specific coverage characteristics suited to different applications.
Apex Canopy Specifications:
Width | Projection | Height | Suitable Door Width |
---|---|---|---|
1040mm | 608mm | 800mm+ clearance needed | Up to 1030mm |
1217mm | 608mm | 900mm+ clearance needed | Up to 1207mm |
1394mm | 608mm | 950mm+ clearance needed | Up to 1384mm |
1570mm | 608mm | 1000mm+ clearance needed | Up to 1560mm |
1747mm | 608mm | 1075mm+ clearance needed | Up to 1737mm |
Low Pitch Apex Options: For properties with limited overhead clearance, our Low Pitch Apex door canopy range provides traditional styling with reduced height requirements.
Width | Projection | Clearance Required | Suitable Door Width |
---|---|---|---|
1080mm | 450mm | 161mm minimum | Up to 975mm |
1339mm | 450mm | 161mm minimum | Up to 1180mm |
1650mm | 450mm | 161mm minimum | Up to 1440mm |
Mono Canopy Range: Our Mono door canopy range offers single-slope designs offering excellent drainage with moderate visual impact.
Width | Projection | Clearance Required | Suitable Door Width |
---|---|---|---|
1050mm | 500mm | 500mm minimum | Up to 1040mm |
1350mm | 500mm | 500mm minimum | Up to 1340mm |
1650mm | 500mm | 500mm minimum | Up to 1640mm |
1950mm | 500mm | 500mm minimum | Up to 1940mm |
2250mm | 500mm | 500mm minimum | Up to 2240mm |
Flat Canopy Specifications: Contemporary door canopy and decorative flat door canopy options requiring minimal overhead clearance.
Width | Projection | Clearance Required | Suitable Door Width |
---|---|---|---|
1200mm | 600mm | 250mm minimum | Up to 1190mm |
1500mm | 600mm | 250mm minimum | Up to 1490mm |
1800mm | 600mm | 250mm minimum | Up to 1790mm |
Choosing the Right Size for Your Application
Optimal sizing balances practical coverage requirements with visual proportions and installation constraints. Generally, canopy width should exceed door width by 150-300mm on each side, providing adequate coverage whilst maintaining pleasing proportions. However, architectural context and exposure levels may justify different approaches.
Coverage Optimization: Consider how you use your entrance when determining coverage requirements. Frequent package deliveries benefit from generous coverage, whilst properties with covered approaches might prioritise visual impact over maximum protection. Exposed locations require deeper projections to provide effective shelter from driving rain.
Proportional Considerations: Canopy size should relate appropriately to your property's scale and architectural character. Substantial Victorian houses can accommodate larger canopies that might overwhelm modest terraced properties. Similarly, generous frontages allow wider canopies that would appear cramped on narrow facades.
Planning and Building Restrictions: UK planning regulations generally permit canopies up to 1000mm projection without specific consent, though local variations and special designations may impose additional restrictions. Always verify local requirements before finalising dimensions, particularly for larger installations or properties in conservation areas.
Custom Sizing Options
Whilst standard sizes suit most applications, some properties require custom dimensions to accommodate unusual door configurations, architectural constraints, or specific design requirements. Our manufacturing capabilities include bespoke sizing within practical limits, ensuring optimal fit for challenging applications.
Custom Applications:
Unusually wide or narrow door openings
Properties with architectural constraints requiring specific dimensions
Matching existing canopies on adjacent properties
Coordinating with planned building alterations
Heritage properties requiring historically appropriate proportions
Technical Limitations: Manufacturing and structural considerations impose practical limits on custom sizing. Excessive widths require additional support, whilst extreme projections may exceed planning limits or create structural challenges. We work with customers to achieve optimal solutions within practical constraints.
Lead Times and Costs: Custom sizing typically extends manufacturing lead times and may involve additional costs compared to standard options. However, the improved fit and performance often justify these considerations, particularly for challenging applications where standard sizes prove inadequate.
Table of Contents
5. Wall Types and Installation Considerations
Successful canopy installation depends fundamentally on understanding your wall construction and selecting appropriate fixing methods. UK building practices have evolved considerably over the decades, creating diverse wall types that require different approaches to achieve secure, long-lasting installations. Modern cavity walls, traditional solid brick construction, stone buildings, and contemporary cladding systems each present unique challenges and opportunities that experienced installers recognise immediately. Our years of manufacturing and supporting installations across the UK have revealed common mistakes that compromise both security and appearance, often stemming from inadequate wall assessment or inappropriate fixing selection. Professional installation companies understand these nuances instinctively, but DIY enthusiasts need clear guidance to achieve comparable results. The consequences of poor fixing selection extend beyond immediate security concerns to include water penetration, structural damage, and warranty invalidation that can prove far more expensive than proper initial installation.
Brick Walls - The UK Standard
Solid brick walls represent the gold standard for canopy installation, offering excellent load-bearing capacity and straightforward fixing procedures. Most UK properties built before 1920 feature solid brick construction that provides reliable support for even substantial canopies when proper techniques are employed.
Installation Advantages: Solid brick provides excellent holding power for appropriate fixings, with minimal risk of unexpected failures when installations follow correct procedures. The consistent material properties allow predictable performance calculations and standard fixing schedules that simplify installation planning.
Best Practices: Always drill into brick rather than mortar joints, which offer significantly reduced holding power and may crumble under load. Use sharp masonry drill bits at appropriate speeds to prevent brick cracking or drill bit wandering. Position brackets to engage multiple brick courses where possible, distributing loads across larger areas.
Fixing Selection: Standard masonry anchors provide excellent performance in solid brick, with through-bolts offering maximum security for heavy canopies. Expanding anchors suit most applications whilst chemical anchors provide maximum holding power for challenging installations.
Cavity Walls - Modern Complexity
Cavity wall construction dominates post-1920 UK building, featuring outer brick leaves backed by inner block work with insulation cavities between. This construction requires longer fixings that engage both leaves for optimal performance, particularly with heavier canopies that generate significant leverage forces.
Understanding Cavity Construction: Typical cavity walls feature 102mm outer brick leaves, 50-100mm cavities, and 100-200mm inner block work. Canopy fixings must penetrate through the outer leaf and achieve adequate engagement with the inner structural wall to provide reliable long-term performance.
Fixing Strategies: Use fixings long enough to penetrate at least 50mm into the inner leaf after passing through the outer brick and cavity. Frame fixings or through-bolts often provide optimal performance, whilst expanding anchors require careful selection to ensure proper engagement with both wall leaves.
Potential Complications: Insulation materials can interfere with fixing performance, whilst cavity barriers may prevent access to inner walls. Modern cavities often contain partial fill insulation that complicates fixing procedures and may require specialist techniques.
Stone Walls - Traditional Challenges
Stone construction presents unique challenges due to material variability, irregular surfaces, and potential structural limitations. Successful stone wall installations require careful assessment of stone type, wall thickness, and fixing compatibility to achieve reliable long-term performance.
Stone Type Considerations: Soft stones like limestone require gentle drilling techniques and may need larger fixings to achieve adequate holding power. Hard stones like granite provide excellent holding power but require carbide-tipped drill bits and patience during drilling operations.
Surface Preparation: Irregular stone surfaces often require packing behind brackets to achieve level, secure mounting. Use appropriate packers and sealants to prevent water penetration whilst maintaining structural integrity.
Fixing Selection: Choose fixings appropriate for specific stone types, with longer anchors often providing better performance in variable materials. Chemical anchors excel in stone applications, providing reliable holding power regardless of minor variations in hole dimensions.
Rendered Walls - Surface Complications
Rendered walls present additional complexity through multiple material layers that require careful consideration during fixing selection and installation procedures. The render thickness, substrate material, and render condition all influence appropriate installation techniques.
Render Assessment: Sound render over solid substrates accepts standard masonry fixings with appropriate length adjustments. However, failing render or render over weak substrates may require render removal and substrate fixing for reliable performance.
Installation Techniques: Drill slowly through render to prevent cracking or spalling that can compromise appearance and weather resistance. Use appropriate sealants around fixings to prevent water penetration that might cause render failure over time.
Repair Considerations: Minor render damage during installation can usually be repaired invisibly, but extensive damage may require professional render repairs that add cost and complexity to installation projects.
Specialist Wall Types
Pebbledash and Roughcast: These textured finishes require surface preparation to create flat mounting areas whilst preserving the overall texture appearance. Careful chipping and local smoothing allow proper bracket seating without extensive damage.
Concrete Panel Construction: Found in some post-war housing, concrete panels require specialist fixings designed for concrete applications. The material's hardness demands powerful drills and patience, but provides excellent holding power when proper techniques are employed.
Timber Frame with Cladding: Modern timber frame construction with brick or rendered cladding requires fixings that engage the structural timber frame rather than relying solely on outer cladding materials. This often necessitates longer fixings and careful frame location.
Bracket Types and Fixing Methods
Gallows Brackets: Traditional L-shaped supports that provide excellent load distribution and suit most wall types. Available in various sizes to accommodate different canopy weights and projection requirements.
Corbels: Decorative supports that offer modest load-bearing capacity suitable for lighter canopies. Often used where visual impact takes precedence over maximum load-bearing capacity.
Hidden Fixings: Concealed mounting systems that provide clean appearances whilst maintaining structural adequacy. Require precise installation but offer superior aesthetics for contemporary applications.
Through-Bolt Systems: Maximum security fixings that penetrate completely through walls, providing excellent load distribution. Require access to wall interiors but offer ultimate reliability for heavy canopies.
Professional vs DIY Installation
DIY Suitability: Standard installations into solid brick or cavity walls suit confident DIY enthusiasts with appropriate tools and reasonable experience. Clear instructions and quality fixings enable successful installations by careful homeowners.
Professional Requirements: Complex wall types, structural concerns, or valuable properties often justify professional installation that includes appropriate insurance coverage and guarantees. Professionals bring experience with unusual situations and access to specialist tools and techniques.
Safety Considerations: Working at height requires appropriate safety equipment and techniques. Ladder safety, tool handling, and electrical awareness all demand attention during installation procedures.
Planning Permission and Building Regulations
Permitted Development: Most canopy installations fall within permitted development rights, requiring no formal planning consent provided dimensional limits are observed. However, special designations or local restrictions may impose additional requirements.
Building Regulations: Simple canopy installations rarely trigger building regulation requirements, but substantial structures or those affecting drainage systems may require approval. When in doubt, consult local building control departments before proceeding.
Conservation Areas and Listed Buildings: Special consent requirements often apply in conservation areas or to listed buildings. Even minor alterations may require formal approval that can significantly extend project timelines.
Table of Contents
6. Matching Your Home's Style and Architecture
Architectural harmony between your canopy and existing building character creates cohesive, attractive results that enhance property value whilst avoiding the discordant appearance that results from inappropriate style matching. Successful integration requires understanding your property's architectural language - the proportional systems, material palette, and detail vocabulary that defines its character - then selecting canopy designs that complement rather than compete with these existing elements. Our experience across thousands of installations demonstrates that homeowners who invest time in architectural analysis achieve far more satisfying results than those who focus solely on canopy styles in isolation. The most successful installations often involve subtle design adjustments that significantly improve integration whilst maintaining the canopy's functional performance. This approach proves particularly important in areas where neighbouring properties share architectural characteristics, as sympathetic design choices can enhance the entire streetscape whilst assertive or inappropriate selections may appear jarring and reduce property values.
Understanding Architectural Periods
Victorian Properties (1837-1901) Victorian architecture embraces decoration, asymmetry, and varied materials that create rich, complex facades requiring canopies that complement rather than compete with existing detail. Bay windows, decorative brickwork, and ornate timber details establish design languages that successful canopies must respect.
Victorian properties benefit from canopies that echo period proportions and detail approaches whilst providing modern performance standards. Apex designs with appropriate bracketing suit most applications, particularly when finished in heritage colours that coordinate with existing paintwork.
Edwardian Properties (1901-1910) Edwardian design represents a reaction against Victorian excess, favouring cleaner lines and more restrained decoration whilst maintaining human scale and natural materials. Properties from this period often feature red brick construction, sash windows, and modest decorative elements that establish more refined design contexts.
Canopies for Edwardian properties should reflect this architectural restraint, avoiding overly elaborate details whilst maintaining appropriate scale and proportions. Simple apex or pitched designs work well, particularly in materials that complement existing colour schemes.
Georgian and Regency Properties (1714-1830) Georgian architecture emphasises mathematical proportions, symmetry, and classical detail derived from ancient architectural principles. These properties require canopies that respect formal compositional rules whilst maintaining the refinement that characterises successful Georgian design.
Portico-style canopies suit grander Georgian properties, whilst simpler apex designs work for more modest examples. Colour choices should favour traditional whites, creams, or heritage colours that maintain period authenticity.
Modern and Contemporary Properties (1930-present) Modern properties embrace diverse architectural approaches from Art Deco influences through International Style minimalism to contemporary sustainable design. This diversity requires careful analysis of specific design characteristics rather than broad generalizations about "modern" architecture.
Flat canopies often suit contemporary properties with strong horizontal emphasis, whilst carefully detailed traditional forms can complement properties that reference historical styles. The key lies in identifying the specific design approach your property employs.
Material Coordination Strategies
Matching Existing Materials Direct material matching creates strong visual continuity but may not always be practical or desirable. Timber canopies naturally suit properties with exposed timber elements, whilst metal details suggest metal canopy frames. However, high-quality alternatives can achieve similar visual effects with superior performance characteristics.
Our composite materials can replicate timber appearances whilst eliminating maintenance requirements that may be impractical for canopy applications. Similarly, powder-coated metals can match existing ironwork colours whilst providing superior corrosion resistance.
Complementary Material Approaches Sometimes contrasting materials create more successful relationships than direct matching attempts. Light-coloured canopies can provide attractive contrast against dark building materials, whilst dark canopies may suit light facades better than attempted matches that never quite succeed.
The key lies in ensuring adequate visual weight balance and avoiding colour combinations that appear jarring or unstable. Natural material combinations often provide safe starting points for successful schemes.
Contemporary Material Integration Modern materials offer opportunities to enhance period properties without compromising authenticity. High-quality composites and advanced coatings can provide period-appropriate appearances whilst delivering contemporary performance that heritage materials cannot match.
This approach particularly suits properties where authentic materials would require impractical maintenance commitments or where exposure conditions exceed traditional material capabilities.
Colour Scheme Development
Traditional Colour Approaches Heritage properties often benefit from traditional colour schemes that respect historical precedent whilst accommodating modern preferences. White and cream remain popular choices that suit most architectural periods whilst providing neutral backgrounds for other facade elements.
Heritage colour ranges offer researched alternatives that enhance period character whilst maintaining broad appeal. These colours often appear more sophisticated than pure whites whilst avoiding bold hues that may date quickly or appear inappropriate.
Contemporary Colour Strategies Modern colour theory offers sophisticated approaches to canopy colour selection that can enhance both traditional and contemporary properties. Neutral greys provide timeless appeal whilst coordinating with diverse material palettes, whilst carefully selected accent colours can create attractive focal points.
The key lies in understanding colour relationships within your property's overall palette, ensuring canopy colours enhance rather than compete with existing elements. Professional colour consultation can prove valuable for challenging applications.
Coordinating with Existing Elements Successful colour schemes often reference multiple facade elements rather than matching single components. Door colours, window frames, guttering, and other details create colour palettes that canopies should acknowledge whilst maintaining their own character.
This approach creates cohesive schemes that appear considered and intentional rather than coincidental. The canopy becomes part of a larger compositional strategy rather than an isolated addition.
Regional Architectural Considerations
Northern England Stone construction dominates many northern regions, creating robust architectural characters that suit substantial canopies capable of withstanding harsh weather conditions. Traditional materials and substantial scales often work better than delicate details that may appear inadequate.
Scottish Architecture Scottish building traditions emphasise weather resistance and robust construction that influences appropriate canopy selection. Stone, slate, and other natural materials create design contexts that favour substantial, well-detailed canopies over lightweight alternatives.
Coastal Regions Salt exposure and extreme weather conditions influence both architectural character and appropriate canopy specifications. Corrosion-resistant materials and robust construction become essential rather than optional considerations.
Conservation Areas Special planning designations often impose additional constraints on canopy design, requiring closer adherence to historical precedent and often involving formal approval processes. Early consultation with planning authorities can prevent costly delays or required modifications.
Style Coordination Guidelines
Traditional Properties:
Respect existing proportional systems
Choose materials that age appropriately
Avoid overly contemporary details that appear anachronistic
Consider maintenance requirements that suit property character
Contemporary Properties:
Embrace clean lines and minimal details
Choose materials that complement modern construction
Avoid fussy traditional details that appear inappropriate
Consider integrated approaches that enhance architectural concepts
Mixed-Period Properties: Many properties combine elements from multiple periods through additions and alterations. These require careful analysis to identify dominant architectural themes whilst acknowledging period diversity.
Transitional Approaches: Sometimes neutral designs that avoid strong period references work better than attempting to match conflicting architectural languages. Quality materials and good proportions can create successful installations that enhance rather than date properties.
Professional Design Assistance
Complex architectural contexts may benefit from professional design advice that can identify optimal approaches whilst avoiding common pitfalls. Architects, conservation specialists, or experienced suppliers can provide valuable guidance for challenging applications.
This investment often proves worthwhile for valuable properties, complex architectural contexts, or situations where planning constraints require sophisticated design responses.
Table of Contents
7. Weather Protection Benefits
British weather patterns create demanding conditions that make effective entrance protection essential rather than optional for most UK properties. Our maritime climate delivers not just the famous frequent rainfall - averaging 150+ wet days annually - but also the driving winds, sudden temperature variations, and atmospheric moisture that gradually degrade unprotected building elements. After manufacturing canopies for thousands of UK homes, we've witnessed firsthand how proper weather protection extends door life, improves daily comfort, and prevents the costly moisture-related problems that plague exposed entrances. Quality canopies must address the full spectrum of weather challenges, from the obvious need to stay dry whilst unlocking doors to the subtle but significant protection against UV degradation that affects even cloudy Britain. The engineering required to create truly effective weather protection goes far beyond simple roof provision - proper drainage, wind resistance, and structural integrity under loading all contribute to systems that perform reliably for decades rather than failing when protection is most needed.
Rain and Moisture Protection
Immediate Shelter Benefits Standing at your front door during a downpour while fumbling for keys becomes a miserable experience that proper canopy design eliminates entirely. Quality canopies provide sufficient coverage to keep occupants dry whilst allowing comfortable access to door hardware, post boxes, and entry systems. The projection depth proves critical - minimal overhangs might deflect vertical rainfall but offer little protection against wind-driven precipitation common in exposed locations.
Preventing Water Damage Beyond personal comfort, effective rain protection prevents moisture penetration that causes door swelling, frame rot, and paint deterioration over time. Wooden doors prove particularly vulnerable, but even composite and uPVC alternatives benefit from reduced moisture exposure that prevents thermal cycling and weathering damage.
Advanced Water Management Our canopy designs incorporate sophisticated drainage systems that channel water away from entrances whilst preventing the dripping and water pooling that characterises inferior products. Integral guttering, concealed drainage channels, and properly designed slopes ensure collected rainwater discharges safely without creating new problems around building foundations.
Preventing Ice Formation Winter protection extends beyond simple rain deflection to preventing the ice formation that makes entrance areas treacherous. Canopy coverage reduces surface moisture that would otherwise freeze on steps and thresholds, whilst thermal protection moderates temperature fluctuations that contribute to ice accumulation.
Wind Resistance and Structural Integrity
Engineering for UK Conditions British weather combines rainfall with significant wind speeds that create challenging loading conditions for exterior structures. Our canopies undergo rigorous testing to ensure they maintain integrity under wind loads that exceed typical storm conditions, providing reliable protection rather than becoming hazards themselves.
Structural Design Principles Effective wind resistance requires more than robust materials - proper structural design distributes loads efficiently whilst maintaining architectural appeal. Our bracket systems and fixing methods reflect engineering analysis that ensures adequate safety margins without unnecessary bulk or visual weight.
Installation Considerations Even excellently designed canopies require proper installation to achieve their protective potential. Wall conditions, fixing selection, and installation quality all influence long-term performance under extreme weather conditions. Our detailed installation guides reflect years of field experience identifying common failure modes and prevention strategies.
Quality Assurance Testing We subject our designs to simulated wind loading that exceeds British Standard requirements, ensuring adequate performance margins under real-world conditions. This testing programme has revealed design improvements that enhance both performance and longevity whilst maintaining manufacturing efficiency.
UV Protection and Material Preservation
Understanding UV Damage in Britain Despite our reputation for cloudy skies, UV radiation in Britain causes significant degradation of unprotected materials over time. Door finishes fade and chalk, timber surfaces crack and weather, whilst even modern composites may show colour changes without proper UV stabilisation.
Comprehensive UV Shielding Quality canopies reduce UV exposure on doors, frames, and surrounding building elements that would otherwise require more frequent maintenance or replacement. This protection proves particularly valuable for south-facing entrances that receive maximum solar exposure throughout the day.
Material Technology Our manufacturing incorporates UV-stabilised materials throughout the canopy structure, ensuring the protective system itself maintains appearance and performance despite constant exposure. UV stabilisers extend throughout material thickness rather than surface treatments that wear away over time.
Colour Retention Performance Advanced pigment systems in our materials resist fading even under intense UV exposure, maintaining appearance for decades rather than requiring refinishing after a few seasons. This performance proves particularly important for homeowners who choose specific colours to coordinate with existing building elements.
Snow Load Management
Structural Capacity British snow loading rarely reaches extreme levels, but occasional heavy falls can impose significant loads on inadequately designed structures. Our canopies incorporate appropriate safety margins whilst maintaining proportions suitable for residential applications.
Snow Shedding Design Pitched canopy profiles naturally shed snow accumulation, preventing the gradual loading increase that might stress inadequate structures. Roof angles and surface finishes encourage snow movement whilst maintaining architectural appeal.
Drainage Considerations Melting snow creates substantial water volumes that drainage systems must accommodate without overflow or backup. Our drainage designs address peak flows that occur during rapid thaw conditions rather than just normal rainfall intensities.
Preventing Ice Dams Proper canopy design prevents ice dam formation that could direct water into building structures or create hazardous falling ice conditions. Thermal breaks and appropriate ventilation maintain conditions that prevent problematic ice accumulation.
Thermal Protection Benefits
Temperature Moderation Canopy coverage moderates temperature extremes that affect door materials and entrance comfort. Reduced thermal cycling extends material life whilst providing more comfortable conditions for entrance activities.
Preventing Thermal Shock Rapid temperature changes stress building materials and may cause cracking or dimensional instability. Canopy protection reduces these effects, particularly on wooden doors and frames susceptible to thermal movement.
Energy Efficiency Contributions Reduced thermal loading on entrance doors contributes modestly to overall building energy efficiency by reducing heat transfer through these typically less-insulated building elements. While not dramatic, these benefits accumulate over heating seasons.
Comfort Enhancement Protected entrances remain more comfortable during extreme weather, encouraging proper door closing and reducing heat loss that occurs when occupants rush through entrance procedures during unpleasant conditions.
Long-term Protection Value
Maintenance Reduction Effective weather protection significantly reduces maintenance requirements for doors, frames, and surrounding building elements. Paint lasts longer, timber requires less frequent treatment, and hardware experiences reduced wear from weather exposure.
Preventing Costly Repairs Water damage, UV degradation, and thermal cycling can necessitate expensive door replacement or frame repairs that far exceed canopy costs. Protection investment prevents these expenses whilst maintaining building appearance and functionality.
Insurance Considerations Some insurance providers recognise weather protection measures in their risk assessments, potentially affecting premiums or claims considerations. While not universal, this recognition acknowledges the genuine protective value that quality installations provide.
Property Value Enhancement Estate agents consistently emphasise the importance of well-maintained entrances in property valuations. Effective weather protection maintains entrance appearance whilst demonstrating property care that appeals to potential purchasers.
Table of Contents
8. Cost Factors & Budgeting
Understanding the complete cost picture for door canopy ownership requires examining not just initial purchase prices but also installation expenses, long-term maintenance requirements, and the value provided through enhanced property appeal and protection. Our experience manufacturing canopies across all price points has revealed that initial cost rarely predicts long-term satisfaction - materials, construction quality, and design appropriateness often prove more significant factors in determining overall value. Budget-conscious homeowners can achieve excellent results through careful product selection and realistic assessment of their priorities, whilst those seeking premium solutions benefit from understanding which features justify additional investment. The UK market offers products spanning from under £100 to several thousand pounds, but this range reflects genuine differences in materials, manufacturing quality, and design sophistication rather than simple markup variations. Smart budgeting involves balancing upfront costs against maintenance requirements, expected lifespan, and the specific benefits most important to your situation.
Material Cost Comparisons
Polycarbonate Solutions: £30-£150 Entry-level polycarbonate canopies offer basic weather protection at minimal cost, making them attractive for budget-conscious homeowners or temporary installations. These products typically feature aluminium or plastic frames with clear or tinted polycarbonate sheets that provide transparency whilst maintaining weather resistance.
Performance Characteristics: Polycarbonate's light weight simplifies installation and reduces structural requirements, whilst impact resistance exceeds glass alternatives. However, UV exposure gradually reduces clarity and may cause yellowing in lower-quality products. Expected lifespan ranges from 10-15 years depending on quality and exposure conditions.
Best Applications: Budget-conscious installations, temporary structures, or applications where light transmission is prioritised over maximum durability. Suitable for covered locations with reduced weather exposure.
Composite and GRP Canopies: £300-£800 Mid-range composite and GRP products represent our core manufacturing focus, offering excellent long-term value through superior materials and construction quality. These canopies combine aesthetic appeal with practical performance that suits most residential applications.
Performance Advantages: Advanced materials resist fading, cracking, and weather damage whilst requiring minimal maintenance throughout their 25-30 year lifespans. Integral colour and sophisticated manufacturing ensure consistent quality and appearance.
Investment Justification: Higher initial costs are offset by reduced maintenance requirements and extended lifespan that provides superior value over ownership periods. Professional appearance enhances property value whilst providing reliable weather protection.
Timber Canopies: £800+ Premium timber canopies offer authentic character and natural beauty that many homeowners find irreplaceable. Hand-crafted details and traditional construction methods justify higher costs whilst providing unique aesthetic qualities.
Hidden Costs: Timber's maintenance requirements include regular treatment, occasional repairs, and eventual replacement of weathered components. These ongoing costs can exceed initial purchase prices over extended ownership periods.
Value Considerations: Timber canopies suit homeowners who appreciate natural materials and accept maintenance commitments. The unique character development and authentic appearance justify premium pricing for appropriate applications.
Size Impact on Pricing
Standard Size Economics Manufacturing efficiency enables competitive pricing for popular sizes that accommodate most residential applications. Our standard range covers 80% of customer requirements whilst maintaining quality standards that ensure long-term satisfaction.
Popular Size Benefits: Standard dimensions benefit from manufacturing economies whilst ensuring compatibility with common UK door configurations. Inventory availability enables faster delivery and simplified customer service.
Size Progression Costs: Larger canopies require proportionally more materials and may need enhanced structural systems that increase costs beyond simple dimensional scaling. Bracket upgrades, reinforced construction, and shipping considerations all contribute to price progression.
Custom Sizing Premiums Special dimensions accommodate unusual applications but typically involve additional costs that reflect manufacturing flexibility and reduced economies of scale. However, proper fit often justifies these premiums through improved performance and appearance.
Custom Applications:
Unusually wide or narrow door openings
Architectural constraints requiring specific dimensions
Coordinating with existing building elements
Heritage properties requiring historical accuracy
Cost Justification: Custom sizing prevents compromise solutions that may appear awkward or provide inadequate protection. The improved results often justify additional costs through enhanced satisfaction and property value.
Installation Cost Considerations
DIY Installation Savings Confident DIY enthusiasts can achieve significant savings through self-installation whilst gaining satisfaction from personal accomplishment. Our products include comprehensive instructions and customer support that enable successful installations by careful homeowners.
How to Stay Safe Installing a Door Canopy
Tool Requirements: Basic tool requirements include drills, levels, measuring equipment, and appropriate safety gear. Most installations require only standard tools available to experienced DIY enthusiasts.
Skill Assessment: Successful DIY installation requires comfort with power tools, working at height, and following detailed instructions. Realistic self-assessment prevents safety risks and installation problems.
Professional Installation Costs: £100-£400 Professional installation provides guaranteed results with appropriate insurance coverage whilst eliminating safety risks and installation stress. Experienced installers complete typical installations in 2-4 hours depending on complexity.
Value Considerations: Professional installation includes expertise in handling wall conditions, unexpected complications, and ensuring proper weatherproofing. Guarantees provide peace of mind whilst eliminating DIY risks.
Cost Factors: Installation costs vary based on wall conditions, access difficulties, and regional labour rates. Complex installations or challenging locations may require additional time and expertise.
Long-term Value Analysis
True Cost Calculation Method Our recommended value assessment divides total ownership costs by guaranteed performance years to reveal genuine cost-per-year figures that enable meaningful comparisons between alternatives.
Example Calculations:
£600 canopy with 10-year warranty = £60 per year
£450 canopy with 2-year warranty = £225 per year
£750 canopy with 15-year warranty = £50 per year
This analysis reveals that premium products often provide superior long-term value despite higher initial costs.
Maintenance Cost Projections Different materials involve varying maintenance requirements that significantly impact long-term ownership costs:
Composite/GRP: £10-20 annually Minimal maintenance requires only occasional cleaning with standard household products.
Timber: £50-100 annually Regular treatment, painting, and repair costs accumulate significantly over time.
Metal: £20-40 annually Inspection and occasional touch-up requirements are modest but necessary for longevity.
Hidden Cost Awareness
Installation Complications Standard installation assumptions may not apply to all properties, potentially creating unexpected costs:
Wall Condition Issues: Damaged render, weak substrates, or access difficulties can increase installation time and costs.
Planning Requirements: Conservation areas or listed building status may require professional drawings or planning applications.
Utility Relocations: Existing lighting, alarms, or other services may require relocation for optimal canopy positioning.
Warranty Considerations Warranty terms vary significantly between suppliers and products, affecting long-term cost calculations:
Coverage Scope: Some warranties cover only manufacturing defects whilst others include material degradation and performance issues.
Installation Requirements: Professional installation may be required to maintain warranty validity, affecting total project costs.
Claim Procedures: Complex warranty claims processes may involve costs and delays that reduce practical warranty value.
Budget Planning Strategies
Priority Assessment Successful budgeting begins with honest assessment of your priorities and circumstances:
Immediate vs Long-term: Budget constraints may favour lower initial costs whilst long-term value suggests premium material selection.
Aesthetic vs Performance: Some applications prioritise appearance whilst others emphasise maximum weather protection.
Maintenance Tolerance: Realistic assessment of maintenance commitment helps guide material selection decisions.
Value Optimization Approaches Several strategies can improve value whilst managing costs:
Timing Purchases: Off-season purchasing may offer savings whilst avoiding peak demand periods.
Bundle Opportunities: Coordinating canopy installation with other exterior work may reduce overall costs.
Quality Focus: Prioritising quality in critical components whilst accepting economy in less important areas can optimise value.
Competitive Analysis
Market Position Understanding Our pricing reflects genuine value through quality materials, advanced manufacturing, and comprehensive customer support rather than premium positioning without substance.
Quality Comparisons: Direct price comparisons often overlook significant quality differences that affect long-term satisfaction and value.
Service Differences: Comprehensive customer support, detailed installation guidance, and responsive warranty service justify modest price premiums.
Performance Verification: Independent testing and quality certifications provide objective validation of performance claims and value propositions.
Competitive Advantages Our manufacturing approach delivers specific advantages that justify our market position:
Material Excellence: Advanced composite formulations and precision manufacturing provide superior performance and longevity.
Design Innovation: Continuous improvement programs incorporate customer feedback and field experience into product development.
Customer Support: Comprehensive technical support and installation guidance ensure successful outcomes regardless of customer experience levels.
Table of Contents
9. Maintenance and Care
Proper maintenance significantly extends canopy lifespan whilst preserving appearance and performance that justifies your initial investment. Our experience supporting thousands of installations has revealed that modest, regular attention prevents the deterioration patterns that necessitate expensive repairs or premature replacement. Most homeowners can perform required maintenance using standard household products and basic tools, making this an accessible way to protect your investment rather than requiring specialist knowledge or equipment. The maintenance approach varies considerably between materials - our composite canopies require minimal attention whilst timber alternatives need regular, skilled care to maintain their attractive appearance and structural integrity. Understanding these requirements helps inform material selection decisions whilst ensuring realistic expectations about long-term care commitments. Neglected maintenance not only accelerates deterioration but may void warranties that provide important protection against unexpected failures or performance issues.
Material-Specific Maintenance Requirements
Composite Canopy Care Our composite canopies are specifically engineered for minimal maintenance whilst maintaining appearance and performance over decades of exposure. The integral pigmentation and advanced material formulation eliminate many traditional maintenance requirements whilst providing superior weather resistance.
Routine Cleaning: Annual cleaning with mild household detergent and warm water removes accumulated dirt, pollen, and atmospheric pollutants that can dull appearance over time. Use soft cloths or sponges to avoid scratching whilst ensuring thorough coverage of all surfaces.
Inspection Schedule: Annual inspection should verify fixing security, check for any impact damage, and ensure drainage systems remain clear. While problems are rare, early detection enables simple repairs rather than costly replacements.
Long-term Performance: Composite materials maintain structural properties throughout their service life without requiring treatment or refinishing. Colour stability ensures consistent appearance without the fading or chalking that affects painted alternatives.
GRP Maintenance Protocols Glass Reinforced Plastic canopies combine exceptional durability with minimal maintenance requirements, making them ideal for homeowners seeking install-and-forget solutions.
Surface Care: Bi-annual cleaning maintains gel coat appearance whilst preventing dirt accumulation that can harbour moisture. Automotive cleaning products work excellently, providing superior results compared to household alternatives.
Gel Coat Protection: Quality gel coats resist UV damage and maintain gloss levels for decades without polishing or refinishing. However, occasional application of appropriate waxes can enhance appearance whilst providing additional UV protection.
Structural Monitoring: GRP's excellent fatigue resistance means structural problems are extremely rare. Annual fixing checks ensure continued security whilst monitoring for any unusual wear patterns.
Timber Canopy Maintenance Timber canopies require the most comprehensive maintenance programmes but reward this attention with unique character development and authentic natural beauty.
Treatment Schedule: Annual inspection should identify areas requiring treatment attention before moisture penetration causes lasting damage. Quality exterior wood preservatives penetrate deeply to provide lasting protection against decay and insect attack.
Refinishing Requirements: Most timber canopies benefit from refinishing every 2-3 years depending on exposure levels and original treatment quality. Preparation proves critical - inadequate surface preparation compromises treatment effectiveness regardless of product quality.
Repair Strategies: Minor timber damage can often be repaired invisibly using appropriate fillers and treatment systems. However, extensive damage may require component replacement that maintains structural integrity whilst preserving appearance.
Winter Protection: Pre-winter inspection and treatment provides crucial protection during the most challenging weather conditions. Pay particular attention to end grain and joint areas where moisture penetration risk is highest.
Seasonal Maintenance Schedules
Spring Preparation Spring cleaning removes winter accumulation whilst identifying any damage that requires attention before summer weather arrives.
Comprehensive Cleaning: Remove leaves, debris, and any organic growth that may have accumulated during winter months. Pay particular attention to drainage areas where blockages can cause water retention problems.
Damage Assessment: Winter weather may have caused minor damage that requires prompt attention to prevent escalation. Check fixing security, surface condition, and structural integrity whilst weather conditions favour outdoor work.
Growth Management: Remove any vegetation growth that might compromise canopy function or appearance. Early attention prevents establishment of persistent growth that becomes difficult to eliminate.
Summer Monitoring Summer's combination of UV exposure, thermal cycling, and occasional severe weather creates specific monitoring requirements.
UV Protection Verification: Check that UV-sensitive materials maintain their protective properties whilst identifying any early signs of degradation that might require attention.
Thermal Movement Accommodation: Verify that expansion joints and flexible connections continue to accommodate thermal movement without stress concentration or failure.
Storm Damage Response: Severe summer storms can cause sudden damage that requires prompt attention to prevent escalation. Post-storm inspection should verify structural integrity and identify any required repairs.
Autumn Preparation Autumn preparation focuses on ensuring canopies are ready for winter's challenges whilst addressing any maintenance requirements identified during summer monitoring.
Drainage Clearance: Remove accumulated leaves and debris that could block drainage systems during winter's heavy rainfall periods. Clean gutters, clear outlets, and verify positive drainage slopes.
Weatherproofing Verification: Check that seals, joints, and weatherproofing systems remain effective before winter's challenging conditions arrive. Address any deficiencies whilst weather conditions favour outdoor work.
Securing Loose Elements: Verify that all components remain securely fastened and that no seasonal movement has created looseness that winter weather might exploit.
Winter Protection Winter's combination of moisture, temperature cycling, and occasional severe weather requires specific attention to vulnerable areas.
Ice Management: Remove ice accumulation that could stress structural elements or create safety hazards. Avoid aggressive removal techniques that might damage surfaces or protective coatings.
Moisture Control: Ensure that drainage systems continue to function effectively despite potential freezing and that accumulated moisture doesn't create problems during freeze-thaw cycles.
Access Maintenance: Keep areas around and beneath canopies clear of ice and debris to maintain safe access whilst preventing slip hazards.
What door canopies need the least maintenance?
Common Problem Identification and Solutions
Water Management Issues Water-related problems represent the most common canopy maintenance challenges, often resulting from blocked drainage or failed weatherproofing.
Drainage Blockages: Leaf accumulation, bird nests, or debris can block drainage systems and cause water retention that stresses structures or creates appearance problems. Regular clearance prevents most issues whilst maintaining effective water management.
Seal Failures: Weatherproofing seals between canopies and walls may deteriorate over time, allowing water penetration that can cause staining or structural damage. Prompt resealing prevents escalation whilst maintaining weather protection.
Surface Ponding: Inadequate slopes or structural settlement can create areas where water accumulates rather than draining properly. Addressing these issues may require professional assessment and structural adjustments.
Fixing and Structural Concerns Canopy fixings must maintain security despite constant loading from weather conditions and thermal cycling.
Bracket Loosening: Thermal cycling and vibration can gradually loosen fixings that appeared secure during installation. Annual checking and retightening prevents most problems whilst maintaining structural integrity.
Wall Movement: Building settlement or movement can stress canopy fixings beyond their design capacity. Professional assessment may be required for significant movement whilst minor adjustments often resolve lesser issues.
Corrosion Concerns: Coastal exposure or industrial atmospheres can accelerate fixing corrosion that compromises structural integrity. Regular inspection enables preventive treatment whilst severe corrosion may require fixing replacement.
Surface and Appearance Problems Maintaining canopy appearance preserves property value whilst indicating overall condition and care levels.
Staining and Discolouration: Atmospheric pollution, organic growth, or water staining can compromise appearance whilst potentially indicating underlying problems. Appropriate cleaning often resolves surface issues whilst persistent problems may require treatment attention.
Impact Damage: Accidental impacts from ladders, equipment, or severe weather can damage surfaces or compromise structural integrity. Prompt repair prevents escalation whilst maintaining appearance and function.
UV Degradation: Inadequate UV protection can cause fading, chalking, or surface deterioration that compromises both appearance and long-term durability. Early recognition enables protective treatment whilst severe degradation may require refinishing or replacement.
Professional Maintenance Services
When to Seek Professional Help While most maintenance tasks suit homeowner attention, certain situations require professional expertise for safety, effectiveness, or warranty compliance.
Structural Concerns: Any signs of structural distress, significant movement, or fixing failures require professional assessment to ensure safety and determine appropriate remedial action. Attempting DIY repairs on structural issues can exacerbate problems whilst creating safety risks.
Complex Repairs: Extensive damage, component replacement, or modifications requiring structural alterations benefit from professional expertise that ensures proper execution whilst maintaining warranty coverage.
Safety Considerations: Working at height, handling heavy components, or addressing electrical integration requires appropriate safety equipment and experience that many homeowners lack.
Warranty Compliance: Some warranty terms require professional maintenance or repairs to maintain coverage validity. Understanding these requirements prevents inadvertent warranty voidance through well-intentioned DIY efforts.
Table of Contents
10. Legal and Regulatory Requirements
UK planning and building regulations establish frameworks that most residential canopy installations navigate successfully without requiring formal approvals, but understanding these requirements prevents costly mistakes and ensures compliance with legal obligations. The permitted development rights that cover most canopy installations include specific dimensional limits and application criteria that determine whether formal planning permission is required. Additionally, building regulations address structural safety and construction standards that apply to more substantial installations, whilst conservation areas and listed buildings impose additional constraints that require careful consideration during planning stages. Our experience across thousands of UK installations has revealed common regulatory pitfalls that careful homeowners can avoid through proper preparation and consultation. Local planning authorities often provide informal guidance that can clarify requirements and prevent expensive misunderstandings, making early consultation a wise investment even for apparently straightforward projects. Understanding these frameworks enables confident decision-making whilst ensuring compliance with obligations that protect both your interests and those of your neighbours and community.
Planning Permission Framework
Permitted Development Rights Most residential canopy installations benefit from permitted development rights that allow construction without formal planning permission, provided specific criteria are met. These rights represent a balanced approach that enables homeowner improvements whilst protecting community interests and planning standards.
Dimensional Limits: Canopies must not extend more than 1 metre from the original wall face, ensuring they remain proportionate to residential properties whilst preventing excessive projection that might affect neighbours or public spaces. Height restrictions limit total structure height to 3 metres above ground level, maintaining reasonable scale whilst accommodating most design requirements.
Application Criteria: Permitted development rights apply only to original dwelling houses, excluding flats, maisonettes, and buildings that have previously extended their permitted development allowances. Commercial properties and mixed-use buildings typically require formal planning permission regardless of canopy size.
Boundary Considerations: Canopies must not extend within 2 metres of any boundary that borders a highway, public footpath, or bridleway, ensuring adequate clearance for public safety whilst preventing obstruction of public spaces.
When Planning Permission is Required Several circumstances trigger formal planning permission requirements that extend project timelines and may involve additional costs.
Dimensional Exceedances: Canopies exceeding permitted development limits require full planning applications that consider visual impact, neighbour amenity, and conformity with local planning policies.
Special Designations: Conservation areas, National Parks, Areas of Outstanding Natural Beauty, and World Heritage Sites often impose additional restrictions that require formal approval even for modest alterations.
Listed Buildings: Any alterations to listed buildings require Listed Building Consent in addition to any planning permissions, creating more complex approval processes that require specialist expertise.
Article 4 Directions: Some areas have specific Article 4 Directions that remove permitted development rights for particular types of alterations, requiring formal planning permission for otherwise permitted works.
Do I Need Planning Permission for a Door Canopy?
Building Regulations Compliance
Structural Requirements Building regulations address structural safety and construction standards that ensure canopies provide adequate performance without creating hazards.
Load-Bearing Capacity: Canopy structures must demonstrate adequate strength to resist anticipated loads including self-weight, wind forces, and snow accumulation. While calculations are rarely required for standard residential canopies, structural adequacy remains a regulatory requirement.
Fixing Standards: Fixings must provide adequate security for anticipated loading whilst ensuring compatibility with wall construction. Inappropriate fixing selection can compromise both performance and regulatory compliance.
Material Standards: Construction materials must demonstrate appropriate durability and performance characteristics for their intended application. Quality assurance and certification provide evidence of regulatory compliance.
Safety Considerations Public safety requirements ensure canopies don't create hazards for occupants or the public.
Height and Clearance: Adequate head clearance prevents injury whilst ensuring emergency access remains unobstructed. Standard residential canopies rarely create clearance problems, but verification ensures compliance.
Structural Stability: Canopies must remain stable under anticipated loading without creating risks from collapse or component failure. Quality installation and appropriate maintenance support ongoing compliance.
Public Safety: Canopies overhanging public areas must consider pedestrian safety and potential liability issues. Professional consultation may be advisable for installations adjacent to public spaces.
Conservation Area and Listed Building Requirements
Conservation Area Constraints Conservation areas impose additional planning controls that preserve architectural and historic character whilst allowing appropriate development.
Design Requirements: Canopy designs must demonstrate compatibility with conservation area character through appropriate materials, proportions, and details that respect the historic environment.
Material Restrictions: Traditional materials or high-quality alternatives that respect historic character may be required, potentially affecting design options and costs.
Approval Processes: Conservation area approval processes often involve additional consultation and specialist expertise that extend timelines whilst ensuring appropriate outcomes.
Listed Building Considerations Listed buildings require Listed Building Consent for any alterations that affect the building's character or historic fabric.
Heritage Impact Assessment: Proposed alterations must demonstrate minimal impact on historic character whilst providing appropriate justification for any changes to historic fabric.
Specialist Expertise: Listed building applications typically require conservation specialists who understand regulatory requirements and can present proposals effectively to planning authorities.
Reversibility Requirements: Alterations may need to demonstrate reversibility without damage to historic fabric, affecting fixing methods and design approaches.
Insurance and Liability Considerations
Home Insurance Implications Canopy installations rarely affect standard home insurance policies, but notification may be advisable to ensure coverage adequacy.
Structural Additions: Some insurers consider canopies as structural additions that require policy notification, particularly for larger or more substantial installations.
Installation Method: Professional installation may provide additional warranty protection and demonstrate due diligence that supports insurance claims if problems arise.
Maintenance Requirements: Insurance coverage may depend on adequate maintenance that preserves structural integrity and prevents foreseeable failures.
Public Liability Concerns Canopies that could affect public areas or neighbouring properties create potential liability issues that require consideration.
Professional Installation: Professional installation typically includes public liability insurance that provides protection against claims arising from installation activities.
Ongoing Maintenance: Adequate maintenance prevents deterioration that could create liability risks from falling components or structural failure.
Documentation: Maintaining records of installation, maintenance, and any professional inspections provides evidence of responsible ownership that supports legal positions if issues arise.
Neighbour Consultation and Rights
Boundary Considerations While most canopy installations don't require formal neighbour consultation, courteous communication can prevent disputes and maintain positive relationships.
Shared Walls: Semi-detached and terraced properties often share structural walls that require careful consideration during canopy installation to prevent damage or disputes.
Visual Impact: Canopies that significantly affect neighbours' outlook or property enjoyment may create grounds for planning objections or disputes.
Drainage Impact: Canopy drainage must not discharge onto neighbouring properties or create additional surface water problems that affect shared areas.
Right to Light Considerations Ancient lights and established windows may have legal protection that canopies must respect.
Impact Assessment: Significant canopies in sensitive locations may require professional assessment to determine whether right to light issues exist.
Mitigation Strategies: Design modifications or alternative solutions may resolve potential conflicts whilst achieving desired weather protection and aesthetic goals.
Legal Consultation: Complex right to light situations may require legal advice to understand obligations and potential liability risks.
Regional and Local Variations
Scottish Planning Systems Scotland operates distinct planning systems that differ in detail from English and Welsh frameworks whilst maintaining similar general principles.
Permitted Development Variations: Scottish permitted development rights include specific provisions that may differ from English equivalents, requiring local verification of applicable limits and criteria.
Conservation Considerations: Scottish conservation frameworks include additional designations and requirements that affect canopy installation approval processes.
Building Standards: Scottish Building Standards provide similar frameworks to English Building Regulations whilst including specific Scottish requirements and procedures.
Welsh Planning Requirements Wales maintains separate planning frameworks that include specific Welsh requirements and procedures.
Language Requirements: Planning applications in Wales may require Welsh language consideration and documentation that affects application processes and costs.
National Park Designations: Welsh National Parks include additional protection levels that may affect canopy installation requirements and approval processes.
Local Authority Variations: Welsh local authorities may impose additional requirements that reflect local planning priorities and conservation objectives.
Local Authority Specific Requirements Individual councils often maintain additional requirements or guidance that affects canopy installation beyond national frameworks.
Design Guides: Many councils publish design guides that establish preferred approaches for residential alterations including canopy installations.
Conservation Policies: Local conservation policies may impose additional requirements or restrictions that affect design options and approval requirements.
Pre-Application Services: Many councils offer pre-application advice services that clarify requirements and identify potential issues before formal applications are submitted.
Table of Contents
11. Installation Process
Professional canopy installation combines technical expertise with practical experience to achieve secure, weather-tight results that maintain appearance and performance for decades. While our canopies are designed for straightforward installation by competent DIY enthusiasts, understanding the complete process helps homeowners make informed decisions about professional versus self-installation whilst ensuring appropriate preparation regardless of approach chosen. The installation sequence progresses logically from initial site assessment through final weatherproofing, with each stage building upon previous work to achieve professional results. Our detailed installation guides reflect years of field experience identifying common challenges and proven solutions that ensure success even for less experienced installers. However, certain situations involving complex wall conditions, challenging access, or valuable properties may justify professional installation that provides guaranteed results with appropriate insurance coverage and expert problem-solving capabilities when unexpected complications arise.
Pre-Installation Site Assessment
Wall Condition Evaluation Successful installation begins with thorough assessment of wall conditions that will support the canopy throughout its service life. This evaluation identifies potential complications whilst ensuring appropriate fixing methods are selected for specific wall types encountered.
Structural Adequacy: Examine wall construction to verify adequate load-bearing capacity for anticipated canopy weights and wind loads. Solid brick walls typically provide excellent support, whilst cavity walls may require longer fixings that engage inner structural leaves. Rendered walls need assessment of render condition and substrate adequacy.
Surface Preparation Requirements: Identify areas requiring cleaning, repair, or preparation before installation begins. Loose render, damaged brickwork, or previous fixing holes may need attention to ensure proper canopy mounting and weather resistance.
Obstruction Identification: Map existing features including lighting, alarm systems, drainage pipes, and utility connections that might affect canopy positioning or require relocation during installation.
Access Planning: Assess access requirements for safe installation including ladder positioning, material handling, and workspace organisation. Identify any obstacles that might complicate installation procedures or require special equipment.
Measurement Verification Accurate measurement ensures proper fit whilst identifying any dimensional issues that require resolution before installation begins.
Critical Dimensions: Verify door opening width, available wall space, overhead clearances, and projection requirements to confirm canopy compatibility with site conditions.
Level Assessment: Check door head levels, wall plumb conditions, and ground slopes that affect canopy installation and appearance. Minor irregularities can usually be accommodated, whilst significant problems may require remedial work.
Bracket Positioning: Mark bracket positions based on canopy requirements and wall conditions, ensuring adequate clearance from obstructions whilst maintaining structural adequacy.
Drainage Planning: Identify water discharge routes and ensure drainage solutions don't create problems for building foundations or neighbouring properties.
How to Stay Safe Installing a Door Canopy
Tool and Equipment Requirements
Essential Installation Tools Quality tools ensure efficient installation whilst achieving professional results that reflect proper preparation and execution.
Drilling Equipment: Hammer drills with appropriate masonry bits provide clean, accurate holes in various wall materials. Bit sizes must match fixing requirements whilst drill power should suit wall hardness and density.
Measuring and Marking: Spirit levels, measuring tapes, and marking tools ensure accurate positioning whilst maintaining proper alignment throughout installation procedures.
Assembly Tools: Socket sets, screwdrivers, and spanners enable secure assembly whilst providing access to confined spaces that may occur during installation.
Safety Equipment: Ladder safety, eye protection, and appropriate work clothing prevent injuries whilst ensuring compliance with safety requirements throughout installation.
Specialised Equipment Considerations Some installations benefit from additional equipment that improves results or addresses specific challenges.
Lifting Assistance: Larger canopies may require additional manpower or mechanical assistance to position safely whilst preventing damage during installation.
Site Protection: Protective coverings prevent damage to landscaping, paving, or building finishes during installation activities.
Weather Protection: Temporary weather protection may be necessary for installations during adverse conditions or where weather exposure could damage ongoing work.
Step-by-Step Installation Procedures
Stage 1: Bracket Installation Bracket installation establishes the foundation for secure canopy mounting whilst ensuring proper alignment and load distribution.
Position Marking: Transfer measurements to wall positions, using spirit levels to ensure brackets will be level and properly spaced. Double-check all measurements before drilling to prevent expensive mistakes.
Drilling Operations: Drill holes to specified depths using appropriate drill bits and techniques for wall materials encountered. Clear debris from holes to ensure proper fixing engagement.
Fixing Installation: Install wall fixings according to manufacturer specifications, ensuring proper torque and engagement without over-tightening that might damage wall materials.
Bracket Mounting: Secure brackets to wall fixings, verifying level installation and proper spacing before final tightening. Check bracket security and stability before proceeding.
Stage 2: Canopy Positioning and Attachment Canopy installation requires careful handling to prevent damage whilst achieving proper alignment and secure attachment.
Lifting and Positioning: Lift canopy carefully to avoid damage, using adequate manpower for safe handling. Position canopy on brackets ensuring proper seating and alignment.
Attachment Procedures: Secure canopy to brackets according to manufacturer specifications, ensuring all connections are properly tightened and seated.
Alignment Verification: Check canopy alignment, level installation, and proper clearances before final tightening of all connections.
Stability Testing: Test installation stability and security without exceeding design loads or creating damage risks.
Stage 3: Weatherproofing and Finishing Final weatherproofing ensures long-term performance whilst achieving professional appearance standards.
Sealant Application: Apply appropriate sealants around wall connections to prevent water penetration whilst maintaining neat, professional appearance.
Drainage Verification: Test drainage systems to ensure proper water management without overflow or backup problems.
Final Inspection: Conduct thorough inspection of installation quality, checking all connections, alignments, and finishes before completing work.
Cleanup and Protection: Remove installation debris and protect finished work until any settling or curing processes are complete.
Common Installation Challenges and Solutions
Wall Condition Complications Unexpected wall conditions can complicate installation but rarely prevent successful completion with appropriate problem-solving approaches.
Weak or Damaged Substrates: Crumbling mortar, weak render, or damaged brickwork may require repair before installation can proceed safely. Sometimes alternative fixing positions avoid problem areas whilst maintaining structural adequacy.
Hidden Obstructions: Electrical conduits, pipework, or structural elements may interfere with planned fixing positions. Alternative positioning or specialist advice may be required to resolve conflicts safely.
Irregular Surfaces: Uneven walls may require packing behind brackets to achieve proper mounting whilst maintaining appearance standards. Quality installations accommodate minor irregularities invisibly.
Technical Difficulties Installation procedures occasionally present technical challenges that require problem-solving skills and appropriate responses.
Access Limitations: Restricted access may require alternative installation sequences or specialised equipment to achieve proper results safely.
Weather Complications: Adverse weather may require work postponement or temporary protection to ensure quality results and installer safety.
Tolerance Issues: Minor dimensional mismatches can usually be accommodated through adjustment or modification without compromising performance.
Professional Installation vs DIY Considerations
DIY Installation Suitability Assessment Honest self-assessment helps determine whether DIY installation is appropriate for specific circumstances and skill levels.
Skill Requirements: Successful DIY installation requires comfort with power tools, working at height, following detailed instructions, and problem-solving unexpected complications.
Time Investment: DIY installation typically requires more time than professional work, including preparation, actual installation, and cleanup activities.
Risk Assessment: Consider safety risks, potential property damage, and warranty implications when deciding between DIY and professional installation.
Support Availability: Evaluate available assistance for lifting, positioning, and problem-solving during installation procedures.
Professional Installation Benefits Professional installation provides several advantages that may justify additional costs for many homeowners.
Expertise and Experience: Professional installers bring experience with various wall conditions, installation challenges, and problem-solving approaches that ensure successful outcomes.
Insurance Coverage: Professional installation typically includes public liability insurance that protects against property damage or personal injury during installation.
Warranty Protection: Some product warranties require professional installation to maintain validity, affecting long-term protection and support availability.
Time Efficiency: Professional installation typically completes more quickly than DIY approaches whilst achieving consistently professional results.
Choosing Installation Professionals Selecting appropriate installation professionals ensures satisfactory results whilst avoiding common pitfalls associated with inexperienced or inadequate contractors.
Qualification Verification: Verify relevant trade qualifications, insurance coverage, and experience with similar installations before engaging professional services.
Reference Checking: Contact previous customers to verify work quality, reliability, and customer service standards before making final decisions.
Quotation Comparison: Obtain multiple quotations that include detailed scope descriptions and completion timelines to enable informed comparisons.
Contract Clarity: Ensure installation contracts clearly define scope, responsibilities, timelines, and warranty terms to prevent misunderstandings or disputes.
How to Stay Safe Installing a Door Canopy
Post-Installation Verification and Commissioning
Initial Performance Testing Systematic testing immediately after installation identifies any issues requiring attention whilst ensuring optimal performance from the beginning.
Structural Security: Verify that all fixings remain secure and that the canopy exhibits no movement or instability under reasonable testing loads.
Weather Protection: Test drainage systems and weather resistance during the first rainfall to ensure proper performance and identify any required adjustments.
Alignment and Appearance: Final inspection of alignment, finish quality, and overall appearance ensures professional results that meet expectations.
Documentation: Record installation details, warranty information, and maintenance requirements for future reference and warranty protection.
Settling Period Monitoring New installations may require minor adjustments during initial settling periods as fixings seat and materials accommodate environmental conditions.
Periodic Checks: Monitor installation stability and alignment during the first few months, checking for any loosening or movement that requires attention.
Seasonal Verification: First winter and summer exposures may reveal performance characteristics requiring minor adjustments or optimization.
Maintenance Planning: Establish maintenance schedules and procedures based on specific installation conditions and material requirements.
Table of Contents
12. Choosing the Right Canopy Supplier
Selecting a reliable canopy supplier significantly influences both your immediate purchasing experience and long-term satisfaction with your installation. The UK market includes manufacturers, distributors, retailers, and resellers whose approaches to quality, customer service, and after-sales support vary dramatically despite superficially similar product offerings. Our position as direct manufacturers provides unique insight into industry practices that affect customer outcomes - from the quality control measures that ensure consistent product performance to the technical support that resolves installation challenges and warranty issues. Successful supplier selection requires looking beyond initial pricing to evaluate manufacturing quality, technical expertise, customer service standards, and the commercial stability that ensures ongoing support throughout your canopy's service life. The lowest initial price rarely provides the best value when installation problems, warranty issues, or premature failure create additional costs and frustration that careful supplier selection easily avoids.
Evaluating Manufacturing Quality and Standards
Understanding Manufacturing Approaches Different suppliers employ varying manufacturing methods that significantly impact product quality, consistency, and long-term performance despite similar appearance in product listings or photographs.
Direct Manufacturing vs Reselling: Direct manufacturers like Apex Canopies control quality from raw materials through finished products, ensuring consistent standards and enabling continuous improvement based on field performance feedback. Resellers depend on third-party manufacturing that may prioritise cost reduction over quality optimisation.
Quality Control Systems: Established manufacturers implement systematic quality control that monitors material properties, dimensional accuracy, and finish quality throughout production. These systems prevent defective products reaching customers whilst ensuring consistent performance standards.
Material Specifications: Quality manufacturers specify premium materials based on performance requirements rather than cost minimisation. UV stabilisers, impact modifiers, and reinforcement systems represent invisible quality factors that determine long-term satisfaction.
Manufacturing Investment: Significant investment in modern manufacturing equipment and facilities indicates commitment to quality and commercial stability that supports ongoing customer relationships.
Verification Methods Several approaches help evaluate manufacturing quality when direct inspection isn't possible.
Facility Information: Legitimate manufacturers provide detailed information about their facilities, capabilities, and quality systems without evasiveness or vague descriptions.
Technical Documentation: Quality manufacturers provide comprehensive technical specifications, installation guides, and performance data that demonstrate thorough product development and testing.
Industry Recognition: Trade association membership, quality certifications, and industry awards indicate recognition by peers and professional evaluation of capabilities.
Customer Feedback: Consistent positive feedback about product quality and durability across multiple review platforms indicates reliable manufacturing standards.
Assessing Technical Expertise and Support
Pre-Sales Technical Consultation Quality suppliers provide knowledgeable technical support that helps customers select appropriate products whilst avoiding common pitfalls that lead to dissatisfaction.
Product Selection Guidance: Experienced suppliers ask relevant questions about your application, site conditions, and requirements to recommend optimal solutions rather than simply promoting high-margin products.
Installation Support: Comprehensive installation guides, technical drawings, and customer support demonstrate commitment to successful outcomes rather than simply completing sales transactions.
Problem-Solving Capability: Quality suppliers address unusual applications, challenging site conditions, or specific requirements through technical expertise rather than refusing difficult applications.
Honest Limitations Assessment: Reliable suppliers acknowledge when their products aren't suitable for specific applications rather than making inappropriate recommendations that lead to problems.
Post-Sales Support Standards Ongoing support availability indicates supplier commitment to customer satisfaction throughout product life cycles.
Installation Assistance: Quality suppliers provide telephone support, additional documentation, or technical consultation when installation challenges arise.
Warranty Administration: Efficient warranty processes and responsive problem resolution demonstrate commercial stability and customer focus that justify supplier selection.
Spare Parts Availability: Long-term spare parts availability ensures ongoing maintenance support whilst indicating manufacturing continuity and commercial viability.
Technical Updates: Suppliers who provide product updates, maintenance guidance, and performance optimization advice demonstrate ongoing commitment to customer success.
Commercial Stability and Reliability Indicators
Business Longevity and Growth Established suppliers with track records of growth and customer satisfaction provide greater confidence in ongoing support availability and commercial viability.
Trading History: Companies with substantial trading histories demonstrate market success and customer satisfaction that supports continued operation.
Financial Stability: Public financial information, credit ratings, and trade references indicate commercial stability that ensures ongoing warranty support and business continuity.
Investment Patterns: Continued investment in facilities, equipment, and product development indicates commercial health and commitment to future operation.
Market Position: Strong market positions reflect customer satisfaction and competitive advantages that support ongoing commercial success.
Customer Service Standards Professional customer service standards indicate overall business quality and attention to detail that extends throughout supplier operations.
Response Times: Prompt responses to enquiries demonstrate adequate staffing and commitment to customer service that continues throughout business relationships.
Communication Quality: Clear, knowledgeable communication indicates professional standards and technical competence that supports successful project outcomes.
Problem Resolution: Efficient problem resolution and customer complaint handling demonstrate commitment to customer satisfaction that extends beyond initial sales.
Accessibility: Multiple communication channels and reasonable availability indicate customer focus rather than minimal service approaches.
Warranty and After-Sales Considerations
Warranty Terms Evaluation Warranty coverage varies significantly between suppliers, affecting long-term value and protection against unexpected problems.
Coverage Scope: Comprehensive warranties cover material defects, manufacturing faults, and performance issues rather than limiting coverage to obvious manufacturing defects only.
Duration Adequacy: Warranty periods should reflect expected product life and provide meaningful protection rather than minimal coverage that expires before potential problems emerge.
Claim Procedures: Straightforward claim procedures indicate customer focus whilst complex or restrictive processes may indicate attempts to avoid warranty obligations.
Exclusion Clarity: Clear warranty exclusions help set appropriate expectations whilst extensive or vague exclusions may indicate poor product confidence or customer service standards.
After-Sales Support Quality Ongoing support availability and quality significantly impact long-term satisfaction and value realisation from your investment.
Technical Consultation: Continued availability of technical advice for maintenance, modifications, or additional requirements demonstrates ongoing customer commitment.
Spare Parts Supply: Long-term spare parts availability ensures ongoing maintenance capability whilst indicating manufacturing continuity and commercial stability.
Service Network: Regional service networks or approved installer programmes provide local support that enhances customer convenience and problem resolution efficiency.
Customer Communication: Proactive communication about product updates, maintenance requirements, or safety issues demonstrates ongoing customer care and professional responsibility.
Price and Value Assessment Framework
Understanding Pricing Structures Different suppliers employ varying pricing strategies that affect both initial costs and long-term value through different service levels and quality standards.
Direct Manufacturing Advantages: Direct manufacturers eliminate distributor margins whilst maintaining superior technical support and warranty backing that provides enhanced value.
Volume Production Benefits: Established manufacturers achieve economies of scale that enable competitive pricing whilst maintaining quality standards that smaller operations cannot match.
Service Integration: Suppliers who include comprehensive service and support within their pricing provide better value than those charging separately for essential services.
Hidden Cost Avoidance: Quality suppliers include all necessary components and provide clear pricing without hidden charges that emerge during ordering or installation.
Value Calculation Methods Total cost of ownership provides more meaningful value assessment than simple initial price comparison between suppliers.
Warranty Value: Extended warranty coverage provides genuine value through reduced risk and enhanced protection that justifies modest price premiums.
Support Inclusion: Comprehensive technical support, installation guidance, and ongoing consultation provide value that reduces overall project costs and stress levels.
Quality Premiums: Superior materials and manufacturing justify price premiums through enhanced durability, appearance retention, and reduced maintenance requirements.
Service Reliability: Reliable delivery, accurate order fulfilment, and responsive customer service provide value through reduced project complications and delays.
Red Flags and Warning Signs
Supplier Credibility Concerns Several warning signs indicate potential suppliers who may not provide satisfactory service or product quality.
Limited Contact Information: Suppliers without complete contact details, physical addresses, or accessible management may not provide adequate support when problems arise.
Unrealistic Claims: Exaggerated performance claims, unrealistic warranties, or prices significantly below market levels may indicate quality compromises or unsustainable business practices.
Poor Communication: Inadequate responses to enquiries, limited technical knowledge, or reluctance to provide detailed information may indicate poor service standards.
Pressure Tactics: High-pressure sales approaches, limited-time offers, or reluctance to allow adequate consideration time may indicate suppliers focused on transaction completion rather than customer satisfaction.
Quality and Service Warnings Additional indicators help identify suppliers who may not meet quality or service expectations.
Limited Product Information: Vague product descriptions, missing technical specifications, or poor-quality documentation may indicate insufficient product development or quality control.
Restricted Warranty Terms: Warranty terms significantly more restrictive than industry standards may indicate poor product confidence or inadequate customer service commitment.
Customer Feedback Patterns: Consistent negative feedback about product quality, delivery problems, or poor customer service across multiple platforms indicates systemic problems.
Commercial Instability: Frequent business name changes, unclear ownership structures, or financial difficulties may affect ongoing support availability and warranty backing.
Making the Final Selection Decision
Criteria Weighting and Evaluation Systematic evaluation of supplier options against weighted criteria ensures decisions reflect your specific priorities and requirements.
Priority Assessment: Determine relative importance of factors including price, quality, service, warranty coverage, and technical support based on your specific circumstances and requirements.
Scoring Systems: Numerical scoring of suppliers against established criteria provides objective comparison methods that reduce emotional decision-making and ensure comprehensive evaluation.
Reference Verification: Contact previous customers to verify claims about quality, service, and satisfaction levels before making final supplier selection decisions.
Trial Orders: Small initial orders may provide insight into supplier capabilities and service standards before committing to larger projects or ongoing relationships.
Decision Documentation and Implementation Systematic decision-making processes provide confidence whilst establishing clear expectations for ongoing supplier relationships.
Decision Rationale: Document selection rationale to guide future supplier relationships and provide reference for performance evaluation over time.
Contract Clarity: Ensure purchase agreements clearly define expectations, responsibilities, and performance standards to prevent misunderstandings or disputes.
Performance Monitoring: Establish supplier performance monitoring to ensure ongoing satisfaction and identify any issues requiring attention or supplier changes.
Relationship Development: Invest in ongoing supplier relationships that provide mutual benefits and enhanced service levels through demonstrated loyalty and professional interaction.
Table of Contents
13. Common Problems and Solutions
Even quality door canopies occasionally experience problems that require attention to maintain optimal performance and appearance. Our extensive experience supporting thousands of installations has revealed predictable problem patterns that typically result from specific causes with proven solutions. Most issues stem from installation errors, inadequate maintenance, or environmental factors that exceed design expectations rather than fundamental product defects. Understanding these common problems and their solutions enables prompt, effective responses that prevent minor issues from escalating into expensive repairs or safety concerns. Proactive problem identification through regular inspection often enables simple preventive measures that eliminate problems before they affect performance or appearance. While some issues require professional attention for safety or warranty compliance, many problems can be resolved by competent homeowners using standard tools and readily available materials.
Structural and Fixing Problems
Bracket Loosening and Movement Thermal cycling, vibration, and weather loading gradually stress canopy fixings, potentially causing loosening that compromises security and creates safety risks.
Symptom Recognition: Visual movement during wind loading, creaking sounds, or visible gaps between brackets and walls indicate fixing problems requiring immediate attention. Regular inspection enables early detection before security becomes seriously compromised.
Underlying Causes: Inadequate initial fixing selection, installation errors, or wall substrate deterioration commonly cause progressive loosening. Expansion and contraction cycles stress fixings beyond their design capacity when installation quality is inadequate.
Solution Approaches: Retightening existing fixings often resolves minor loosening when wall substrates remain sound. However, enlarged holes or substrate damage may require fixing replacement or alternative fixing positions. Upgrading to larger or more sophisticated fixing systems prevents recurrence.
Prevention Strategies: Annual fixing inspection and prompt attention to minor loosening prevents progression to serious security problems. Quality initial installation with appropriate fixings reduces long-term maintenance requirements.
Wall Substrate Deterioration Building movement, moisture penetration, or age-related deterioration can compromise wall substrates that support canopy installations.
Problem Identification: Cracking render, spalling brickwork, or movement around fixing points indicates substrate problems requiring assessment before they compromise canopy security.
Assessment Requirements: Professional structural assessment may be necessary when substrate problems extend beyond cosmetic surface issues or when building movement is suspected.
Repair Strategies: Minor substrate repairs often enable continued canopy use with minimal disruption. However, extensive problems may require canopy removal during remedial building work.
Long-term Prevention: Addressing underlying moisture problems, maintaining building weather protection, and periodic structural maintenance prevent most substrate deterioration.
Water Management and Drainage Issues
Drainage System Blockages Leaf accumulation, debris, or organic growth can block drainage systems and cause water retention that stresses structures whilst creating appearance problems.
Problem Recognition: Water ponding, overflow during rainfall, or staining around drainage outlets indicates blocked or inadequate drainage requiring immediate attention.
Common Causes: Seasonal leaf fall, bird nesting, or gradual debris accumulation commonly blocks gutters and downpipes. Inadequate drainage slopes may contribute to ongoing problems.
Cleaning Procedures: Regular gutter cleaning and debris removal prevents most blockages whilst ensuring effective water management throughout the year. Access safety requires appropriate equipment and techniques.
System Improvements: Gutter guards, improved slopes, or enlarged drainage capacity may be necessary for problem locations experiencing frequent blockages.
Water Penetration and Leaks Failed seals, structural movement, or design inadequacies can allow water penetration that damages buildings whilst compromising canopy effectiveness.
Leak Detection: Water staining, damp patches, or actual water penetration during rainfall indicates weatherproofing failures requiring prompt attention to prevent escalation.
Seal Assessment: Inspect all joints between canopies and walls, checking sealant condition and adhesion. Failed sealants require removal and replacement with appropriate materials.
Remedial Sealing: Quality exterior sealants provide effective leak prevention when properly applied to clean, prepared surfaces. Colour-matched sealants maintain appearance whilst providing weather protection.
Design Modifications: Persistent leaks may require design modifications including improved drainage, enhanced sealing systems, or structural adjustments to prevent recurrence.
Surface and Appearance Problems
Cleaning and Staining Issues Atmospheric pollution, organic growth, and general weathering can compromise canopy appearance whilst potentially indicating underlying problems.
Stain Identification: Different staining patterns indicate specific causes requiring targeted treatment approaches. Organic stains differ from atmospheric pollution and require different cleaning methods.
Cleaning Techniques: Mild detergent solutions remove most general soiling without damaging surfaces. Specialised cleaners may be necessary for specific stain types or stubborn contamination.
Prevention Strategies: Regular cleaning prevents stain accumulation whilst enabling early detection of potential problems. Protective treatments may reduce staining susceptibility on vulnerable materials.
Professional Restoration: Severely stained or damaged surfaces may require professional restoration to achieve satisfactory appearance and prevent ongoing deterioration.
Surface Damage and Deterioration Impact damage, UV exposure, or material fatigue can compromise surface condition whilst potentially affecting structural integrity.
Damage Assessment: Evaluate damage extent to determine whether cosmetic treatment or structural repair is required. Minor surface damage often accepts simple repair whilst structural damage requires professional attention.
Repair Techniques: Surface scratches, minor cracks, or small holes can often be repaired using appropriate filler materials and refinishing techniques that restore appearance and weather resistance.
Material Limitations: Different materials accept different repair approaches. Composite and GRP materials often enable invisible repairs whilst timber may require more extensive refinishing.
Professional Requirements: Extensive damage or structural concerns require professional assessment to ensure safe, effective repairs that maintain long-term performance.
Weather-Related Damage
Storm Damage Assessment and Response Severe weather can cause sudden damage requiring prompt assessment and appropriate response to prevent escalation or safety problems.
Immediate Safety: Assess canopy security immediately after severe weather, checking for loosened components or structural damage that might create safety hazards.
Damage Documentation: Photograph damage before any repairs for insurance purposes whilst documenting the extent and nature of problems requiring attention.
Temporary Measures: Secure loose components and provide temporary weather protection if necessary whilst arranging appropriate permanent repairs.
Professional Assessment: Significant storm damage may require professional structural assessment to ensure adequate repair and confirm ongoing safety.
UV Degradation and Fading Prolonged UV exposure can cause colour changes, surface deterioration, and material weakening that affects both appearance and performance.
Recognition Signs: Colour fading, surface chalking, or material embrittlement indicates UV damage requiring assessment and potential treatment or replacement.
Treatment Options: UV-damaged surfaces may accept protective treatments that arrest deterioration whilst improving appearance. However, severely damaged materials may require replacement.
Prevention Strategies: Quality UV-stabilised materials resist degradation whilst protective treatments may extend service life of susceptible materials.
Replacement Considerations: Extensively UV-damaged canopies may require replacement with UV-resistant alternatives that provide long-term performance without ongoing treatment requirements.
Maintenance-Related Issues
Inadequate Maintenance Consequences Neglected maintenance allows minor problems to escalate into serious issues that compromise performance, appearance, and potentially safety.
Problem Progression: Understanding how minor problems develop into serious issues helps justify maintenance investment whilst enabling appropriate intervention timing.
Cost Implications: Preventive maintenance costs significantly less than corrective repairs or premature replacement that result from neglected problems.
Performance Impact: Inadequate maintenance compromises weather protection, appearance, and structural integrity that reduces the benefits justifying initial canopy investment.
Warranty Implications: Some warranty terms require adequate maintenance to remain valid, making maintenance essential for ongoing protection rather than optional care.
Maintenance Planning and Implementation Systematic maintenance approaches prevent most problems whilst enabling early detection and treatment of emerging issues.
Schedule Development: Regular maintenance schedules based on material requirements and local conditions ensure adequate care without excessive effort or cost.
Skill Requirements: Most maintenance tasks suit homeowner capability with basic tools and appropriate safety equipment. However, some tasks may require professional expertise.
Record Keeping: Maintenance records demonstrate care levels whilst providing valuable information for warranty claims or professional consultations.
Problem Prevention: Proactive maintenance prevents most problems whilst enabling early intervention that minimises repair costs and maintains performance.
Upgrade and Improvement Opportunities
Performance Enhancement Options Existing canopies can often be upgraded or enhanced to improve performance, appearance, or functionality without complete replacement.
Drainage Improvements: Enhanced drainage systems, gutter guards, or improved water management can resolve persistent problems whilst extending canopy life.
Appearance Updates: Refinishing, colour changes, or detail modifications can update appearance whilst maintaining structural adequacy and weather protection.
Functionality Additions: Lighting integration, additional weather protection, or accessibility improvements can enhance utility whilst preserving existing investment.
Material Upgrades: Component replacement with superior materials can improve performance whilst maintaining overall canopy integrity and appearance.
Replacement Considerations Sometimes canopy replacement provides better long-term value than extensive repairs or modifications to inadequate existing installations.
Cost-Benefit Analysis: Compare repair costs, performance limitations, and ongoing maintenance requirements against replacement options that provide superior long-term value.
Technology Improvements: Modern materials and manufacturing techniques offer significant performance improvements that may justify replacement rather than repair of older installations.
Design Evolution: Architectural changes, improved requirements, or enhanced product availability may favour replacement with designs that better suit current needs.
Professional Consultation: Complex decisions between repair and replacement benefit from professional assessment that considers all relevant factors and provides objective recommendations.
Table of Contents
14. Frequently Asked Questions
Our customer service experience across thousands of installations has revealed consistent questions that reflect common concerns, misconceptions, and information needs among UK homeowners considering door canopy installation. These frequently asked questions span technical specifications, regulatory requirements, installation procedures, and long-term ownership considerations that influence purchasing decisions and installation planning. Rather than providing brief, superficial answers, we've developed comprehensive responses that address underlying concerns whilst providing practical guidance based on our manufacturing expertise and field experience. This approach helps customers make informed decisions whilst avoiding common pitfalls that can lead to dissatisfaction or installation problems. The questions are organised by topic to enable efficient information location whilst cross-references guide readers to relevant detailed information throughout this guide.
Planning Permission and Regulatory Questions
Do I need planning permission for a door canopy?
Most residential door canopy installations in England and Wales benefit from permitted development rights that allow installation without formal planning permission, provided specific criteria are met. These provisions recognise that modest entrance improvements serve legitimate homeowner needs whilst maintaining reasonable planning controls.
Your canopy installation is likely permitted development if it meets these requirements:
Projects no more than 1 metre from the original wall face
Remains below 3 metres total height above ground level
Doesn't encroach within 2 metres of boundaries adjoining highways or public footpaths
Applies to the original dwelling house (not flats, maisonettes, or previously extended properties)
However, several circumstances trigger planning permission requirements:
Conservation areas, National Parks, Areas of Outstanding Natural Beauty, and World Heritage Sites often impose additional restrictions
Listed buildings require Listed Building Consent for any alterations
Article 4 Directions in some areas remove permitted development rights
Canopies exceeding dimensional limits require full planning applications
Scotland and Northern Ireland operate separate planning systems with similar general principles but different specific requirements. Always verify local requirements with your planning authority, as variations exist between councils and special designations may impose additional constraints.
What about listed buildings and conservation areas?
Listed buildings require Listed Building Consent for any alterations that affect the building's character or historic fabric, regardless of size or visual impact. This requirement applies even to minor additions like door canopies that might otherwise be permitted development.
Listed Building Consent applications require specialist expertise to demonstrate minimal heritage impact whilst providing appropriate justification for proposed alterations. Conservation officers assess proposals against heritage value, architectural significance, and cumulative impact on the historic environment.
Conservation areas impose additional planning controls designed to preserve architectural and historic character. While permitted development rights often remain valid, some areas have Article 4 Directions that require planning permission for alterations that would normally be permitted. Additionally, conservation area policies may influence appropriate materials, colours, and design details.
Applications in conservation areas and for listed buildings typically require:
Heritage impact assessments demonstrating minimal adverse effects
Detailed drawings showing proposals in context
Materials specifications appropriate to historic character
Evidence of community consultation where required
Professional advice from conservation specialists or experienced architects proves valuable for these applications, as inappropriate submissions can result in refusal and costly resubmission requirements.
Installation and Technical Questions
Can I install a door canopy myself?
Most of our canopies are designed for straightforward installation by competent DIY enthusiasts with appropriate tools and reasonable experience. Our detailed installation guides reflect years of field experience identifying common challenges and proven solutions that enable successful DIY installation.
DIY installation suitability depends on several factors:
Comfort with power tools, particularly hammer drills for masonry work
Experience working safely at height with appropriate ladder techniques
Ability to follow detailed instructions whilst problem-solving unexpected complications
Access to necessary tools including drills, levels, measuring equipment, and safety gear
Availability of assistance for lifting and positioning larger canopies
Standard installations into solid brick or cavity brick walls suit most DIY capabilities when adequate preparation and care are exercised. Our customer support team provides telephone assistance for installation questions and can guide customers through challenging situations.
However, certain circumstances favour professional installation:
Complex wall types including stone, cladding, or structural concerns
Valuable properties where installation errors could cause expensive damage
Challenging access conditions requiring specialised equipment or techniques
Homeowners uncomfortable with height work or power tool operation
Warranty requirements specifying professional installation
Professional installation typically costs £100-£400 depending on complexity and regional labour rates, providing guaranteed results with insurance coverage and expert problem-solving when complications arise.
What tools do I need for installation?
Successful DIY installation requires specific tools and equipment that ensure safe, efficient work whilst achieving professional results:
Essential Tools:
Hammer drill with appropriate masonry drill bits (typically 8-12mm depending on fixing requirements)
Spirit level (minimum 600mm, preferably 1000mm for accurate alignment)
Measuring tape and pencil for marking positions
Socket set or spanners for bracket assembly and tightening
Safety equipment including eye protection and appropriate work clothing
Sturdy ladder with safe positioning and adequate height capacity
Helpful Additional Equipment:
Detector for identifying hidden pipes or electrical cables
Vacuum cleaner for removing drilling debris from holes
Sealant gun and appropriate exterior-grade sealant
Additional assistance for lifting and positioning larger canopies
Material Requirements: Our canopies include all necessary fixings for standard masonry installations. However, alternative wall types may require different fixings available from builders' merchants. Consult our technical support team if uncertain about appropriate fixings for your specific wall construction.
Tool hire represents a cost-effective option for equipment you're unlikely to need again, whilst purchasing quality tools proves worthwhile for homeowners planning additional DIY projects.
What type of wall can support a door canopy?
UK construction methods create diverse wall types that require different installation approaches whilst generally providing adequate support for residential door canopies.
Solid Brick Walls (pre-1920s construction): Excellent load-bearing capacity suits all canopy types when proper fixings and installation techniques are employed. Standard masonry anchors provide reliable performance when positioned in brick rather than mortar joints.
Cavity Brick Walls (post-1920s construction): Modern cavity construction requires longer fixings that engage both outer brick leaves and inner structural blockwork. Quality installations use fixings long enough to penetrate at least 50mm into inner walls after crossing cavities.
Stone Walls: Natural stone provides excellent strength but requires careful drilling techniques and may need surface preparation for level bracket mounting. Stone hardness varies significantly, affecting drilling equipment requirements.
Rendered Walls: Render thickness and substrate condition influence fixing selection and installation procedures. Sound render over adequate substrates accepts standard approaches with appropriate length adjustments.
Specialised Construction: Timber frame with cladding, concrete panels, or other specialist construction may require specific fixing types or professional installation to ensure adequate performance.
Our technical support team can advise on appropriate fixing methods for unusual wall types, whilst professional installation may be prudent for complex or valuable properties where installation errors could cause expensive damage.
How long does installation take?
Installation duration varies based on canopy size, wall conditions, installer experience, and site-specific factors, but typical residential installations complete within predictable timeframes.
Standard Installation Times:
Small to medium canopies (up to 1400mm): 1-2 hours for experienced installers
Larger canopies (1400mm+): 2-4 hours depending on size and complexity
DIY installations: Add 50-100% to professional times for less experienced installers
Factors Affecting Duration:
Wall condition and substrate type influence drilling time and complexity
Access conditions affect setup time and working efficiency
Weather conditions may require protective measures or work postponement
Unexpected complications occasionally require problem-solving and additional time
Preparation Requirements: Proper preparation including tool gathering, measurement verification, and site clearing can significantly reduce actual installation time whilst improving results quality.
Professional installers achieve faster completion through experience, appropriate tools, and efficient work methods, whilst DIY installations benefit from careful preparation and realistic time allowances that prevent rushed work and installation errors.
Material and Maintenance Questions
Which material requires the least maintenance?
Composite and GRP materials offer the lowest maintenance requirements whilst providing excellent long-term performance and appearance retention that justifies their popularity among homeowners seeking install-and-forget solutions.
Composite Polymer (Our Speciality): Our advanced composite formulations require only occasional cleaning with mild detergent and water to maintain appearance throughout their 25-30 year service life. The integral pigmentation resists fading whilst impact resistance and weather protection eliminate most traditional maintenance concerns.
GRP (Glass Reinforced Plastic): Quality GRP canopies maintain appearance and performance for 30+ years with minimal care beyond periodic cleaning. The gel coat finish resists UV damage whilst providing consistent appearance without refinishing requirements.
Maintenance Comparison by Material:
Composite/GRP: Annual cleaning, occasional inspection (£10-20 annually)
Aluminium: Periodic cleaning, occasional touch-ups (£20-40 annually)
Timber: Regular treatment, annual maintenance, periodic refinishing (£50-100 annually)
Steel: Inspection, touch-up painting when required (£30-50 annually)
The significant maintenance savings with composite and GRP materials often offset higher initial costs within a few years, providing superior long-term value for homeowners prioritising convenience and predictable ownership costs.
How do I clean my door canopy?
Proper cleaning maintains appearance whilst enabling inspection for potential problems requiring attention. Cleaning requirements vary by material but generally involve straightforward procedures using common household products.
General Cleaning Approach:
Remove loose debris with soft brush or cloth
Wash with warm soapy water using mild household detergent
Rinse thoroughly with clean water to prevent detergent residue
Dry with soft cloth if necessary to prevent water marking
Material-Specific Considerations:
Composite and GRP: Avoid abrasive cleaners or scouring pads that might scratch surfaces
Timber: Use appropriate wood cleaners and allow thorough drying before applying any treatments
Metal: Check for corrosion during cleaning and address any issues promptly
Cleaning Frequency: Most canopies benefit from bi-annual cleaning, typically in spring and autumn when seasonal debris accumulation is highest. Properties in polluted areas or under trees may require more frequent attention.
Professional Cleaning: Difficult access, extensive staining, or valuable properties may justify professional cleaning services that provide thorough results without homeowner safety risks.
Do timber canopies need regular treatment?
Timber canopies require regular maintenance to preserve their attractive appearance and structural integrity throughout their service life. This maintenance commitment suits homeowners who appreciate natural materials and accept ongoing care requirements.
Treatment Schedule:
Annual inspection for signs of wear, damage, or treatment failure
Treatment renewal every 12-18 months depending on exposure and product quality
Immediate attention to any damage or wear before moisture penetration occurs
Treatment Types: Quality exterior wood preservatives provide protection against moisture, UV damage, and insect attack whilst maintaining natural wood appearance. Transparent stains allow grain visibility whilst opaque treatments offer maximum protection with colour consistency.
Application Requirements: Successful treatment requires thorough surface preparation including cleaning, sanding if necessary, and complete coverage of all exposed timber surfaces. Weather conditions during application significantly affect treatment effectiveness and durability.
Professional Options: Some homeowners prefer professional timber maintenance that ensures optimal results whilst eliminating the time commitment and skill requirements for DIY treatment.
Long-term Considerations: Properly maintained timber canopies can provide 20+ years of service whilst developing attractive weathered patinas. However, neglected maintenance leads to deterioration that may require expensive repairs or premature replacement.
Cost and Value Questions
How much do door canopies cost?
Door canopy pricing reflects genuine differences in materials, manufacturing quality, design sophistication, and included services rather than arbitrary markup variations across the UK market.
Price Ranges by Material and Quality:
Budget polycarbonate systems: £30-£150 (basic weather protection)
Quality composite and GRP canopies: £300-£800 (optimal value and performance)
Premium timber canopies: £800+ (traditional character with maintenance requirements)
Specialist materials (glass, premium metals): £600-£1200+ (architectural statement pieces)
Factors Affecting Pricing:
Material specifications and manufacturing quality significantly impact costs
Size progression involves more than linear scaling due to structural requirements
Design complexity including brackets, details, and finishes affects pricing
Included services such as delivery, fixings, and technical support add value
Hidden Cost Considerations:
Installation costs (£100-£400 professional, £0 DIY with appropriate skills)
Planning applications or building control fees for complex installations
Ongoing maintenance requirements that vary dramatically between materials
Potential repair or replacement costs related to quality and warranty coverage
Value Assessment Approach: Divide total anticipated costs by expected service years to calculate annual ownership costs that enable meaningful comparisons between alternatives. This approach often reveals that premium materials provide superior long-term value despite higher initial costs.
Are there hidden costs I should know about?
Transparent pricing helps customers budget accurately whilst avoiding the surprise charges that can significantly exceed initial estimates.
Commonly Included: Our pricing includes canopies, standard masonry fixings, delivery to UK mainland addresses, and comprehensive technical support throughout the installation process.
Potential Additional Costs:
Specialist fixings for unusual wall types (typically £10-30)
Highland and island delivery surcharges (varies by location)
Professional installation if preferred over DIY (£100-£400)
Planning applications for complex situations (£200+ plus consultant fees)
Building modifications if required for optimal installation
Maintenance Cost Planning:
Composite/GRP materials: Minimal ongoing costs beyond occasional cleaning
Timber canopies: Annual treatment costs of £50-100 plus periodic repairs
Metal canopies: Occasional touch-up requirements and periodic inspection
Insurance and Warranty: Most home insurance policies don't require notification for standard canopy installations, whilst our warranties provide comprehensive coverage without additional charges or restrictive claim procedures.
Comparison Shopping Advice: Verify exactly what's included in quotations from different suppliers, as apparent savings may disappear when missing components, delivery charges, or limited support are considered.
What warranty do you offer?
Our comprehensive 10-year manufacturer's warranty reflects confidence in our materials, manufacturing quality, and design adequacy whilst providing genuine protection against unexpected problems.
Coverage Scope: Our warranty covers manufacturing defects, material degradation, structural integrity issues, and UV stability problems that affect performance or appearance during normal use.
What's Excluded: Damage from improper installation, misuse, accidental impact, or normal wear from inadequate maintenance falls outside warranty coverage, emphasising the importance of proper installation and basic care.
Claim Procedures: Contact our customer service team with details and photographs of any problems. We provide prompt assessment and appropriate remedial action including parts supply or replacement as necessary.
Installation Requirements: Installation according to our provided instructions maintains warranty validity whether completed professionally or through competent DIY work. Professional installation isn't mandatory but may be advisable for complex situations.
Industry Comparison: Our 10-year warranty significantly exceeds typical 1-2 year coverage offered by many suppliers, reflecting superior materials and manufacturing confidence whilst providing meaningful long-term protection.
No Registration Required: Warranty coverage begins automatically from purchase date without registration requirements, though retaining purchase documentation enables efficient claim processing.
Design and Customisation Questions
Can I customise my canopy design?
Our manufacturing capabilities include extensive customisation options that enable optimal solutions for challenging applications whilst maintaining quality standards and competitive pricing.
Standard Customisation Options:
Size modifications within practical manufacturing limits
Colour selection from our standard range or custom colour matching
Bracket style choices including gallows brackets, corbels, or hidden systems
Roof finish options including various tile effects and textures
Advanced Customisation:
Bespoke sizing for unusual door configurations or architectural requirements
Special colours to match existing building elements or specific design schemes
Modified details to suit particular architectural styles or planning requirements
Integration with lighting, signage, or other entrance features
Design Consultation: Our technical team can advise on optimal approaches for challenging applications whilst ensuring solutions remain practical for manufacturing and installation.
Lead Time Implications: Standard products typically ship within 10-14 days whilst custom options may require 4-6 weeks depending on complexity and current production schedules.
Cost Considerations: Customisation costs vary based on complexity and departure from standard specifications. However, improved fit and appearance often justify additional investment through enhanced satisfaction and property value.
How do I choose the right style for my home?
Successful style selection balances architectural compatibility, practical requirements, and personal preferences whilst avoiding common mistakes that lead to inappropriate installations.
Architectural Assessment: Examine your property's design language including proportional systems, material palette, and detail vocabulary to identify appropriate canopy characteristics.
Period Property Guidelines:
Victorian/Edwardian: Traditional apex designs with appropriate bracket details
Georgian: Classical proportions with refined detailing and heritage colours
Modern/Contemporary: Clean lines with minimal ornamentation and neutral colours
Mixed styles: Neutral designs that don't conflict with diverse architectural elements
Practical Considerations:
Available wall space and overhead clearances affect size and style options
Exposure conditions may favour particular materials or design approaches
Maintenance preferences influence material selection and detail complexity
Budget constraints affect available options whilst value considerations guide selection
Professional Guidance: Complex architectural contexts benefit from professional design advice that identifies optimal approaches whilst avoiding common selection errors.
Our technical team can provide guidance based on photographs and site descriptions, helping customers select appropriate styles that enhance rather than compromise their property's character.
This comprehensive guide provides the foundation for informed door canopy selection, installation, and ownership throughout the UK. For specific questions not addressed here, our technical support team at 01684 649523 or enquiries@apexcanopies.co.uk provides expert guidance based on decades of manufacturing experience and thousands of successful installations.
© 2024 Apex Canopies. This guide represents our accumulated expertise in door canopy manufacturing and installation across the UK market. All information is provided in good faith based on current industry standards and regulatory requirements, though individual circumstances may require specific professional consultation.